El mantenimiento predictivo – GENERALIDADES
1 – El mantenimiento predictivo – GENERALIDADES
mantenimiento predictivo , en general, es el tema tratado en este artículo..
La forma más sencilla de operar las máquinas es dejarlas trabajar hasta que se detengan debido a una avería y luego repararlas para que estén en condiciones para un nuevo período de servicio.. Esta práctica puede resultar muy cara en términos de pérdidas de producción y costes de mantenimiento., además de poner en peligro la seguridad de las personas y el medio ambiente..
Ahora se acepta generalmente que, en el caso de unidades con grandes inversiones de capital, es más satisfactorio desde el punto de vista económico, implementar acciones de mantenimiento regulares. Estas, implican la revisión de máquinas o sus componentes a intervalos regulares, para reducir la probabilidad de que se produzcan averías durante el período en el que el equipo está disponible. El principal problema a superar en la implementación de este tipo de mantenimiento, radica en elegir el intervalo de tiempo adecuado, entre reseñas. Efectivamente, el intervalo en el que la acción de mantenimiento se vuelve esencial no es constante, variando de una ocasión a otra, debido a diferencias en las condiciones de servicio y el comportamiento de los componentes.
La figura muestra el comportamiento de un grupo de máquinas. “típico” si no se realiza el mantenimiento preventivo. En otras palabras, el patrón típico de ocurrencia de fallas, en Mantenimiento Curativo.
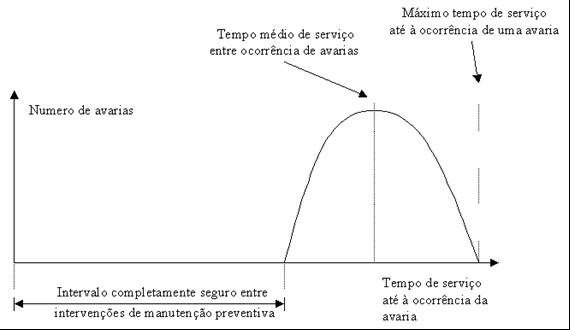
Se puede ver que hay un intervalo de tiempo seguro., entre reseñas, para evitar todas las averías antes de que puedan ocurrir. sin embargo, si eliges este intervalo, Las intervenciones se llevarán a cabo mucho antes de que sean realmente necesarias.. existirá, por lo tanto, muchos casos en los que las máquinas podrían funcionar durante más tiempo sin averías. Esta práctica desperdicia el tiempo de servicio y aumenta la frecuencia de las intervenciones., aumenta la incidencia de errores humanos en los montajes.
Un enfoque más satisfactorio, en términos económicos, es realizar un mantenimiento preventivo, a intervalos que pueden ser irregulares, hacer que las intervenciones dependan del estado de funcionamiento de las máquinas. Para realizar este mantenimiento “bajo condicion”, también llamado "Mantenimiento predictivo", Es fundamental conocer el estado operativo del equipo y su evolución en el tiempo. Para hacer esto, es necesario tener un sistema de control de condición que proporcione este conocimiento..
Este enfoque considera cada máquina individualmente. Reemplazo de revisiones a intervalos fijos, por inspecciones a intervalos fijos, Se puede seguir de cerca la evolución de las condiciones de funcionamiento de cada máquina..
El axioma básico del mantenimiento predictivo es que las máquinas solo se intervienen cuando los resultados de la inspección muestran que es necesario.. Esto también está de acuerdo con la sensibilidad de la mayoría de las personas de que no es prudente manipular máquinas que funcionan bien..
Por ejemplo, con medición regular de los niveles de vibración de una bomba, se pueden detectar los síntomas de mal funcionamiento y seguir su desarrollo.. Los resultados de la medición se pueden extrapolar para predecir cuándo se alcanzarán niveles inaceptables y, por lo tanto, cuando debe intervenir, como se muestra en la figura siguiente..

2 – VENTAJAS DEL MANTENIMIENTO PREDICTIVO
2.1 – Ventajas económicas del mantenimiento predictivo
Las ventajas económicas del mantenimiento predictivo generalmente aparecen de la siguiente manera:
- 2/3 de las ganancias de la reducción de pérdidas de producción
- 1/3 beneficios de la reducción de los costes de mantenimiento
Estas proporciones corresponden a:
- Reducción de las pérdidas de producción correspondientes a 75% de días perdidos anualmente cuando no se utiliza el mantenimiento predictivo
- Reducción en 5% del costo total de mantenimiento
La razón por la que solo puedes esperar 75% de reducción de pérdidas de producción, es que algunos tipos de averías, independientemente de ser detectado, requieren que se detenga la producción. Por otro lado, No se puede esperar que el control de condición sea 100% eficiente.
El número de 5% para la reducción de costos de mantenimiento surge del hecho de que la mayoría de los ahorros se encuentran en el costo de mano de obra de mantenimiento curativo. Dado que el costo de la reparación curativa es generalmente de alrededor 1/3 el costo total de mantenimiento y estos, 1/3 ser costos laborales, el costo de la mano de obra en el mantenimiento curativo es de aproximadamente 10% hacer total. Reducir a la mitad da el número de 5%.
En la siguiente figura, se ordenan los diferentes tipos de industria., en orden ascendente de susceptibilidad, de que haya ganancias con el mantenimiento predictivo. (resultados de un estudio realizado en Gran Bretaña en 1978)

A continuación se muestran algunos ejemplos de aplicaciones de mantenimiento predictivo..
ejemplo 1 – Proceso industrial / Refinería
La siguiente figura muestra el número de paradas por problemas en máquinas rotativas en una refinería..
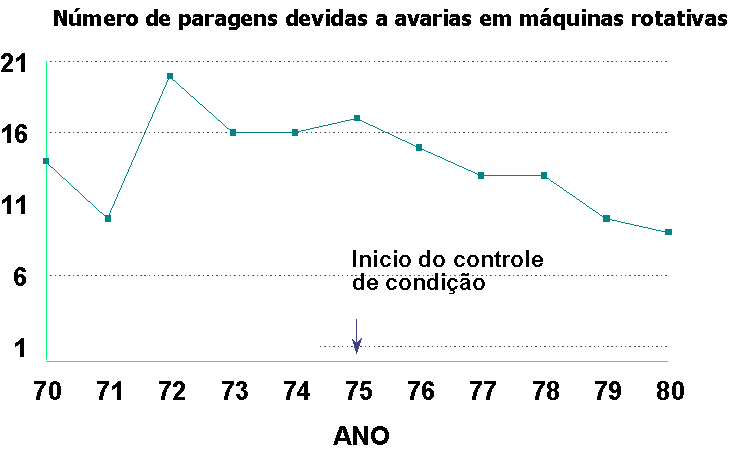
En la siguiente figura, puede ver la cantidad promedio de horas necesarias para comenzar debido a la maquinaria giratoria en una refinería..
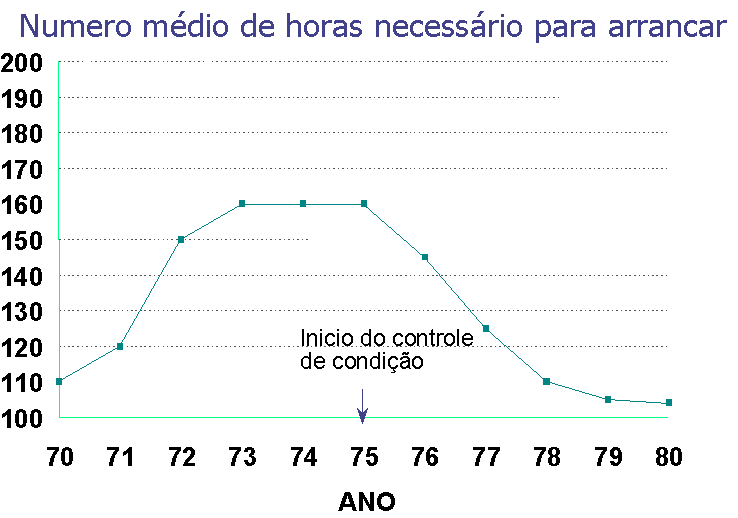
ejemplo 2 – Taller de reparación de motores eléctricos
La siguiente figura muestra la tasa de fallas en las pruebas de motores eléctricos después de la revisión.. En 1978 se implementó un programa de aceptación del motor después de la revisión..
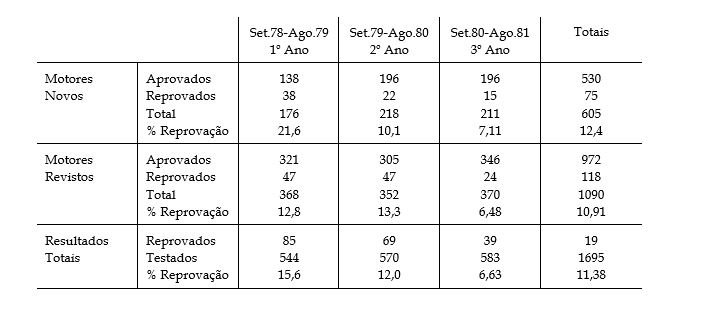
Nótese la fuerte caída en el número de motores en mal estado, a lo largo de los años.
1978 | 1981 | |
Motor electrico Muchachos Tiempo extraordinario Costo de mano de obra por año Contratos externos por año | 1171 7 20% $ 462 000 $ 1 272 000 | 2300 3 despreciable $ 150 000 $ 860 000 |
ejemplo 3 – Costo de mantenimiento por caballo por año – Generación de energía
La siguiente figura muestra el costo de mantenimiento por caballo por año en la industria de generación de energía..

ejemplo 4 – Paradas por averías en máquinas rotativas, en dos máquinas de papel
La siguiente figura muestra el número de paradas debidas a averías en máquinas rotativas en dos máquinas de papel., antes y después de iniciar un programa de mantenimiento predictivo.
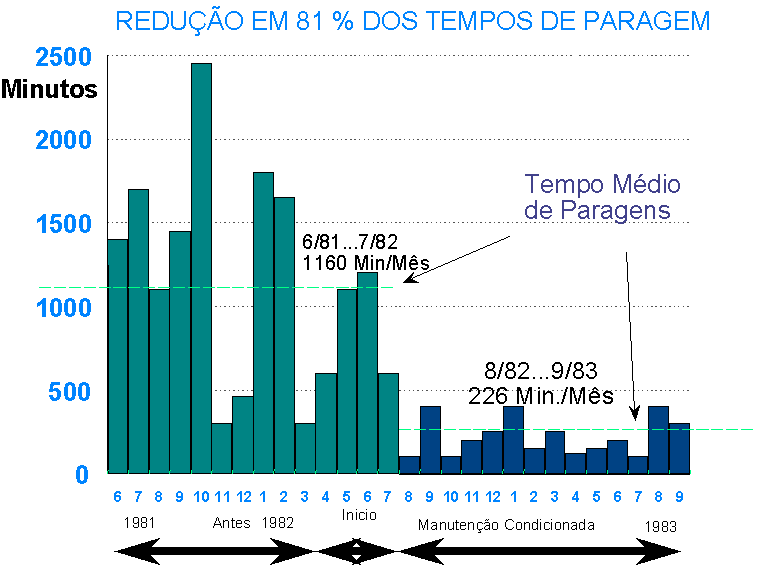
2.2 – Otras ventajas del mantenimiento predictivo
Las ventajas económicas no son el único punto de vista válido a considerar a la hora de implementarlo., o no, un sistema de control de condición. Dado que hay varias ventajas, en cada caso concreto existirán factores especialmente favorables o desfavorables para el Mantenimiento Predictivo.
Estos se enumeran en las tablas que siguen..
QUADRO I
Controlar el estado de las máquinas puede proporcionar los siguientes beneficios | forma en que aparecen los beneficios |
1) Mayor seguridad para el operador de la máquina | El tiempo de advertencia dado por el control de condición permite detener las máquinas antes de llegar a un estado crítico., especialmente si no pueden detenerse instantáneamente |
2) Aumentar la disponibilidad de equipos resultando en una mayor producción a partir del capital invertido. 3) Reducir los costos de mantenimiento | El tiempo de servicio de la máquina se puede aumentar maximizando el tiempo entre revisiones. La duración de la revisión se puede acortar porque se conoce la naturaleza del problema., los repuestos y el personal están disponibles.. Los daños resultantes de un mal funcionamiento se pueden reducir o eliminar. |
4) Mayor eficiencia en la conducción de instalaciones, lo que permite ajustar el volumen de producción a las condiciones de las instalaciones, y lograr un nivel de calidad estable | La carga y la velocidad de algunas máquinas se pueden variar para obtener un buen compromiso entre el tiempo de producción y servicio hasta la próxima mejora. |
5) Mayor capacidad de diálogo con los fabricantes de maquinaria y equipo o reparar, basado en el conocimiento obtenido a partir de la condición de control | La inspección de equipos nuevos, al final de la garantía y después de la revisión proporciona una base útil para la comparación |
6) Mejores relaciones con los clientes debido a la reducción de las paradas de producción no planificadas | Tiempo de advertencia antes de la avería, obtenido a través de la información proporcionada por las inspecciones., permite que esto suceda |
7) Posibilidad de mejorar la especificación y el diseño de futuras instalaciones | El historial obtenido a través de las inspecciones se puede utilizar para este propósito. |
Factores favorables para la aplicación, mantenimiento predictivo exitoso, en una fabrica, maquina o equipo.
QUADRO II
Donde exista un riesgo de seguridad asociado con un mal funcionamiento de la máquina | Ejemplos típicos son las fábricas que trabajan con productos peligrosos y medios de transporte de personas. |
Donde se requiere una planificación de mantenimiento rigurosa | Ejemplos típicos son equipos en ubicaciones remotas que solo se visitan ocasionalmente para mantenimiento, o equipo móvil que solo realiza visitas ocasionales a su base de soporte |
Donde la fábrica o el equipo es un proyecto nuevo donde aún quedan algunos problemas de desarrollo | La inspección permite detectar averías al principio, mientras que el daño es leve, para que la información importante esté disponible para orientar las mejoras al proyecto |
Donde las máquinas de alto costo, sujeto a riesgos de daños importantes, son operados por personal no capacitado o de forma remota | El control de condición le permite detectar el problema con suficiente tiempo de advertencia para emitir instrucciones para poner el equipo fuera de servicio., antes de que ocurra un daño grave |
Donde el fabricante del equipo puede ofrecer un servicio de control de condición a varios usuarios del equipo. | Por tanto, se puede reducir el coste para cada usuario., y el fabricante recibe comentarios importantes para dirigir el diseño y desarrollo de su producto |
Donde la instrumentación u otro equipo requerido para la inspección es, o ya esta siendo, usado para otro propósito | Otra aplicación de instrumentación o equipo puede ser el control de procesos u otras actividades como el balanceo o el diagnóstico. |
3 – FACTORES DE FALLA
Factores que son desfavorables para la aplicación exitosa del Mantenimiento Predictivo, a una fabrica, maquina o equipo.
CUADRO III
Donde la industria tiene una carga ligera y la fábrica o la máquina se detiene con frecuencia | Si la fábrica se detiene con frecuencia, En general, existen muchas oportunidades de inspección y mantenimiento durante el tiempo de inactividad. |
Donde el grupo de máquinas similares es demasiado pequeño para permitir la acumulación de experiencia necesaria para la interpretación efectiva de las lecturas y la correcta toma de decisiones sobre su significado. | Acumular experiencia en un período de tiempo razonable., el número mínimo suele variar entre 4 una 10 dependiendo del tipo de máquina o componente. El problema se puede resolver compartiendo los servicios de inspección con otras fábricas., involucrando a los fabricantes de máquinas o servicios externos |
Donde los operadores altamente calificados tienen un estrecho contacto con sus máquinas, y pueden usar sus sentidos para resolver un sesgo subjetivo | Las máquinas herramienta y los barcos pueden ser un ejemplo de esta situación., pero cualquier paso hacia el uso de operadores menos calificados, favorece la aplicación de mantenimiento predictivo |
Donde se realicen intervenciones en maquinaria o equipos móviles en algunos centros donde se instale mano de obra especializada | La función principal del control de la condición en estas circunstancias es determinar las prioridades de las intervenciones en las diferentes unidades.. Mantenimiento predictivo en este caso, tiene un efecto económico reducido, a menos que pueda resultar en una mejora del proyecto o un mayor rendimiento, y, por lo tanto, dar lugar a una reducción en la frecuencia de las intervenciones y los costos |
4 – CONTROL DE ESTADO
Básicamente, existen dos métodos para realizar el control de condición.:
- Monitoreo tendencia;
- Comprobar el estado de trabajo
El monitoreo de tendencias consiste en mediciones periódicas o continuas, de un parámetro que indica variaciones en las condiciones de funcionamiento de la máquina o sus componentes. lo, por lo tanto, evidente, que es necesario proceder con la selección de indicadores significativos de deterioro de la máquina o componentes, como se indican en la página siguiente.
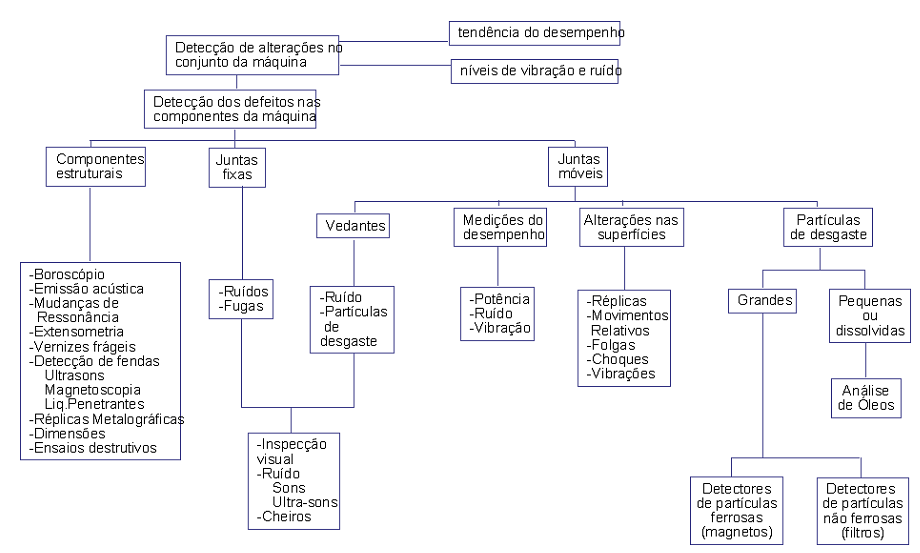
Sobre la base de los valores medidos, prepara una tendencia para determinar cuando la degradación de una máquina supera un estado crítico, como se muestra en la imagen.
Los principios involucrados se ilustran en la siguiente figura., que muestra los medios por los cuales el seguimiento de tendencias puede dar un tiempo de advertencia antes de que el deterioro alcance un nivel en el que la máquina debe ser puesta fuera de servicio.

El tiempo de advertencia antes de que se produzca el fallo, es una de las principales ventajas de utilizar el seguimiento de tendencias en lugar de alarmas o relés de protección..
Comprobando la condición, tiene lugar a través de la medición de un parámetro, en un momento determinado, inferir de ese modo la máquina de estado. Para ser efectiva, la medida tiene que ser precisa, valores medidos deben límites también ser conocidas que no deben superarse durante más de un cierto número de horas de funcionamiento. los límites, que se establecerá, requieren una amplia experiencia previa con el tipo particular de máquina en cuestión. Una comprobación de la condición es, por lo tanto, menos flexible que la tendencia-siguiente, especialmente en relación con el tiempo de advertencia antes de la falla.
Puede ser, sin embargo, muy útil en situaciones en las que hay varias máquinas trabajando juntas, visto en este caso, Se pueden hacer comparaciones entre máquinas en servicio y máquinas que son nuevas o que se sabe que están en buenas condiciones..
Estos dos métodos de control de condición se comparan con más detalle en la siguiente tabla..
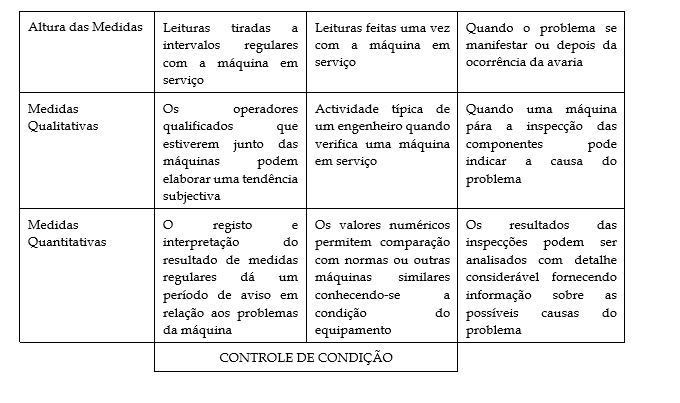
5 – LAS FALTAS
en su forma más simple, desglose, se puede definir como cualquier modificación en una pieza o componente de una máquina que le impida realizar su función de manera satisfactoria..
Los estados habituales que preceden a una ruptura final son, “ruptura incipiente”, “daño incipiente”, “deterioro” mi “daño”, cualquiera de ellos, lo que puede hacer que la pieza o el componente sean poco fiables o inseguros para el servicio.
Las fallas también se pueden clasificar de la siguiente manera:
- deficiencias de diseño
- Defectos materiales
- Defectos de fabricación
- Defectos de montaje
- Condiciones de servicio fuera del proyecto
- deficiencia de mantenimiento
- Errores de operación
La siguiente tabla muestra los tipos básicos de modos de falla que se encuentran en 99% de roturas en equipos en unidades petroquímicas.
Clasificación de modos de falla
- Deformación – el plastico, elástica, etc..
- Fractura – ranuras, fatiga, picaduras, etc..
- Modificaciones de superficie – ranuras, cavitación, desgaste, etc..
- Cambios de material – Contaminación, corrosión, desgaste, etc..
- Desplazamientos – desapertos, holguras excesivas, etc..
- Fugas
- Contaminaciones
modo de fallo, no confundir con causas de mal funcionamiento, porque el primero es el efecto y el segundo la causa. El modo de falla también puede ser consecuencia de una larga cadena de causas., Está hecho, finalmente conduce a una avería funcional, esto es, Un síntoma, un problema o insuficiencia operacional que se refiere a una pieza de equipo como una sola entidad.
Los medios básicos de avería en componentes y piezas de la máquina son siempre la fuerza., hora, temperatura y medio ambiente, como se indica en la tabla siguiente.
Causas de rotura de componentes y piezas de la máquina
Fuerza | estática cíclica transitoria | Temperatura | bajo ambiente transitorio estacionario cíclico alto |
Clima | muy corto corto largo | Ambiente | químico nuclear |
Desde el punto de vista de la inspección, las averías se reflejan en diversas deficiencias.
En la siguiente tabla se enumeran los síntomas típicos de averías en el equipo de proceso.
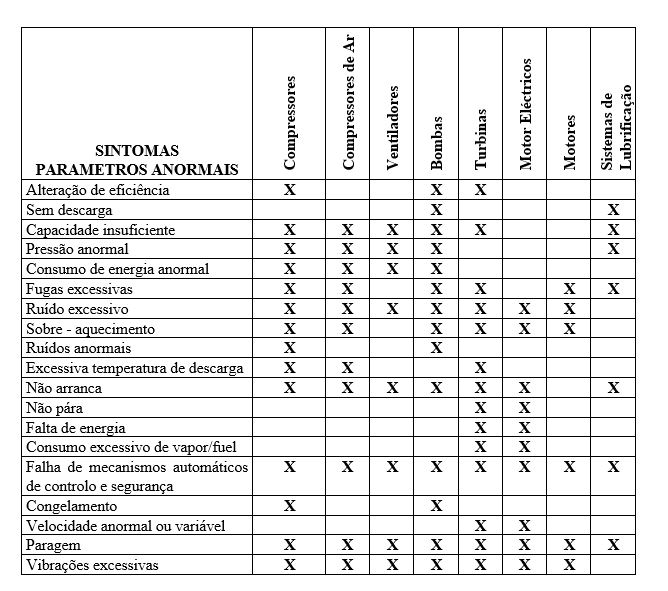
La función de la inspección es monitorear el equipo para detectar los síntomas de mal funcionamiento.
6 – TÉCNICAS DE CONTROL DE ESTADO
La base de un sistema de control de condición son las acciones de inspección que se llevan a cabo regularmente en la maquinaria y el equipo..
estas acciones, donde no solo están en juego los sentidos del inspector, sino también una serie de técnicas específicas, Su objetivo es determinar la evolución de las condiciones de operación del equipo.
Entre las técnicas de inspección existentes, puede hacer referencia, por ejemplo, a lo siguiente:
- Nivel global
- Choques
- Espectro de frecuencia
– Control de desgaste
- Análisis de aceite
- Detectores de partículas
- Ferrografia
– Control de temperatura
- Termometria
- termografía
– Control de ruido
– Control de fugas
Cada uno tiene ventajas y defectos, más allá de sus propias limitaciones. Su aplicación implica, por lo tanto, un conocimiento de todos los factores en juego, Es común aplicar más de una técnica en cada máquina, ya sea como un parámetro a seguir una tendencia, desee comprobar la condición.
Al seleccionar una técnica de control para una máquina crítica, Es importante tener en cuenta que las máquinas funcionaron mal porque uno o más componentes críticos fallan.
Siendo así, los métodos más sensibles para inspeccionar una máquina, funcionan detectando síntomas de mal funcionamiento en componentes individuales., ya que la mayor desviación de las condiciones normales se concentra en estos síntomas, lo que facilita la detección de la anomalía.
Por tanto, la selección de un método de control depende del tipo de componentes más susceptibles a fallar y de cómo ocurre esto.. Entonces se podrán considerar posibles hipótesis para controlar la degradación de estos componentes e incluso será posible encontrar una técnica única que pueda detectar todos los tipos de fallos probables en una máquina con una eficiencia razonable..
Por otro lado, La situación específica de mantenimiento de cada unidad industrial impondrá algunas limitaciones en la elección de las técnicas de inspección a implementar..
Específicamente en el caso de equipos dinámicos, los diversos métodos de inspección se pueden agrupar de la siguiente manera.
1 – Las máquinas de control sensorial se inspeccionan utilizando los sentidos humanos
2 – Control de rendimiento La condición de una máquina o componente se mide por la forma en que realiza su función..
3 – Control de vibraciones La condición de los componentes en movimiento se mide por el tamaño y el tipo de vibraciones generadas..
4 – Control de partículas El estado de las superficies de los componentes críticos, sujeto a cargas y movimientos relativos, se evalúa recogiendo y examinando las partículas de desgaste generadas.
Los cuatro métodos de control mencionados, son usados, detectar la existencia de un problema a través del nivel general de la medida, y en la tasa de cambio, mientras que la naturaleza del problema generalmente se puede determinar a partir de un análisis más detallado de los resultados de la medición.. Esto se describe en la tabla siguiente..
Los métodos de control descritos, son de hecho un medio de comunicación entre la máquina y la persona a cargo del control de condición. inspección visual, en relación con los otros métodos, requiere una preparación técnica mínima, debido a que se realiza a través de los sentidos del inspector. En otros métodos, los medios se utilizan más allá de los sentidos humanos, haciendo las intervenciones más complejas.
También debe tenerse en cuenta que siempre se deben utilizar., de preferencia, parámetros no intrusivos en sistemas, o sea, que no interfieran con el proceso de la máquina y que, si es posible, se obtengan durante su funcionamiento.
Referencias
1 – Métodos y economía de monitoreo de condición, Bruel & Kjaer
2 – Gestión práctica de maquinaria para plantas de proceso VOL.2, Análisis y resolución de problemas de maquinaria, Heinz P. Bloch, Fred K. Geitner, Golfo P. do.