Implementação da monitorização de vibrações
Aqui apresenta-se como se procede a implementação da monitorização de vibrações, para manutenção preditiva.
1 -INTRODUÇÃO – IMPLEMENTAÇÃO DA MONITORIZAÇÃO DE VIBRAÇÕES
Pode‑se afirmar que o objetivo próximo da implementação de um sistema de inspeção das máquinas é a criação de um canal de informação que permita aos centros de decisão da manutenção, definir as ações a realizar, também, em função do estado das máquinas. No dia a dia encontram‑se, pelas mais diversas razões, situações em que esta linha de informação funciona deficientemente ou pura e simplesmente não existe.
Assim face aos elevados custos que isto pode acarretar surge a necessidade da implementação do sistema de inspeção. Uma das maneiras disto ser efetuado consiste em incumbir alguém da função de detetar as avarias antes destas provocarem consequências gravosas.
As situações de monitorização em permanência ainda são raras e só se encontram praticamente nas maiores unidades industriais. Assim na esmagadora maioria dos casos é efetuada uma visita à máquina, utilizando‑se tradicionalmente os sentidos humanos como ferramenta básica.
O controle sensorial que é, na maioria das situações, uma parte essencial de um sistema de inspeção, apresenta, no entanto, duas limitações básicas:
‑ subjetividade
‑ limitações inerentes aos sentidos humanos
Surge assim a necessidade de utilizar equipamentos que ultrapassem estas limitações. A implementação de um sistema de inspeção trata assim basicamente de aspetos relacionados com a utilização de técnicas específicas e da inserção numa organização da manutenção dos resultados das inspeções.
Como é evidente por detrás de isto terá de existir a vontade de implementar o sistema, ou dito por outras palavras, existir uma justificação para a sua existência.
2 -A MOTIVAÇÃO PARA A IMPLEMENTAÇÃO DA MONITORIZAÇÃO DE VIBRAÇÕES
Quando se parte para a implementação de um sistema de controle de condição têm de existir sempre motivos bem claros para isso:
- Aumento da segurança
- Redução de custos de manutenção
- Aumento das disponibilidades dos equipamentos, etc.
À partida estes objetivos devem ser bem quantificados para se poder aferir objetivamente do sucesso (ou insucesso) do sistema. Só o cumprimento regular de objetivos bem claros permitirá assegurar a médio/longo prazo o sucesso do sistema. É esta avaliação objetiva que permitirá manter o sistema a funcionar independentemente das diversas pessoas envolvidas. Estes objetivos podem ser postos em diversos termos:
- Redução do número de pedidos de intervenção devidos a avarias,
- Redução do número de horas extraordinárias;
- Redução do número de horas de paragem devidas a avarias em equipamentos críticos;
- Redução do orçamento em paragens anuais;
- Ganhos obtidos pela deteção de avarias em equipamentos críticos, incluindo custos de reparação e paragem das instalações.
É difícil exagerar a importância desta clara definição de objetivos. É ela que vai permitir a adequada motivação de todos os níveis de gestão para o programa. Esta motivação, não sendo condição suficiente para o sucesso do sistema é, sem margem de dúvida, condição necessária.
3 -IMPLEMENTAÇÃO DA MONITORIZAÇÃO DE VIBRAÇÕES
3.1 – Introdução
A seguir vão‑se abordar os aspetos que se consideram essenciais para a implementação de um sistema de Manutenção Condicionada, a saber:
- ‑Seleção de máquinas e equipamentos a controlar
- -Definição de avarias a detetar em cada máquina
- -Definição de técnicas de acompanhamento da condição para cada equipamento.
- ‑Equipamento de medida e sistema de tratamento de informação
- ‑Procedimentos de medida
- ‑Definição de Níveis de Alarme
- -Planeamento das inspeções e construção de percursos
- ‑Formação e sensibilização
- ‑Organização
Como é evidente tudo o que vai ser referido é feito tendo presente o caso concreto da medição de vibrações nos equipamentos dinâmicos. Todavia, muitos destes aspetos são de âmbito geral e, portanto, não perdem a validade quando aplicados noutras circunstâncias para além da presente.
3.2 – Máquinas e equipamentos a controlar na implementação da monitorização de vibrações
Não é comum englobar no programa de controlo de condição todas as máquinas de uma instalação. Assim regra geral as máquinas onde se vai fazer uma manutenção em função da sua condição obedecem aos seguintes critérios:
- A máquina é crítica para a produção
- A máquina é crítica para a qualidade
- A máquina tem custos de manutenção elevados
- A máquina é crítica para a segurança
- O deficiente funcionamento da máquina tem efeitos negativos no ambiente
- – É economicamente viável controlar a condição da máquina
As máquinas deverão ser categorizadas de acordo com uma hierarquia baseada na criticidade da máquina para o funcionamento da instalação fabril. A tabela a seguir é um método de categorização desenvolvido pela indústria petroquímica. O programa de monitorização periódica deverá focar-se inicialmente em A e B.
Tabela – Classificação das máquinas para monitorização.
Classificação das Máquinas | Resultado da avaria |
A. Crítica | Paragem ou falha inesperada causará perda significativa de produção |
B. Crítica ou propensa a avaria | Paragem ou falha inesperada reduz, mas não interrompe a produção |
C. Crítica com sobresselentes | Serviço leve- causa perturbação na operação, mas não interrupção da produção; custos de reparação justificam algum nível de monitorização |
D. Não crítica | Produção não será afetada pela perda; custo de reparação não justifica monitorização |
Dependendo dos recursos disponíveis, as máquinas na classe C podem ser incluídas no programa posteriormente. Por exemplo, cada instalação fabril tem as suas máquinas de classe A – turbinas e compressores para a indústria petroquímica, geradores de turbina para as indústrias produtoras de energia e máquinas de produzir papel para a indústria de pasta e papel. Uma falha inesperada de um único componente pode resultar na perda de milhões de euros devido a paragem de produção.
Também deve ser dada atenção as máquinas críticas para o ambiente ou segurança.
3.3 Conhecimento das máquinas na implementação da monitorização de vibrações
O conhecimento das características das máquinas é essencial para a condução de uma análise de vibração eficiente.
Quanto mais informação disponível houver acerca do projeto, construção, suportes, respostas operacionais e respostas a defeitos, mais fácil será o diagnóstico de defeitos e de mau funcionamento. Sobre todo o equipamento abrangido deverão ser listados os seguintes dados:
- Características gerais tais como frequência de rotação, de engrenamento, de passagem de palhetas, e frequências de defeito dos rolamentos;
- Vibração, gradientes de temperatura, ou pressão iniciados por um componente operacional ou sistema;
- Respostas de vibração a alterações de processo;
- Características identificadas com o tipo específico de máquina;
- Frequências naturais conhecidas e formas de modo de vibração;
- Sensibilidade à instabilidade causada por desgaste ou alterações nas condições de funcionamento;
- Sensibilidade à vibração causada por desequilíbrio de massa, desalinhamento, distorção, e outras excitações de mau funcionamento/defeito;
Algumas respostas, que se podem ver na tabela A, incluindo vibração, temperatura, e pressão podem ser relacionadas com os componentes do sistema; por exemplo, chumaceiras (rolamento ou de metal antifricção); cilindro de equilíbrio de um compressor centrífugo; disposição das lâminas e engrenamento e rodas dentadas. As frequências e as suas componentes, incluindo bandas laterais, indicam a existência de um defeito e a sua origem. As velocidades dos veios modulam, usualmente, as frequências centrais dos rolamentos e passagem de pás. As amplitudes das bandas laterais e frequências centrais fornecem informação acerca da severidade. Leituras de temperatura e pressão podem estar presentes como componentes DC.
Tabela – Fontes de excitação em componentes das máquinas
Componente | Frequência |
Rolamentos | Frequência de passagem de corpos rolantes – Pista exterior Frequência de passagem de corpos rolantes – Pista interior Frequência da gaiola Frequência da unidade rotativa Frequência de rotação dos corpos rolantes |
Chumaceiras de metal antifricção | Frequência fracionária frequências de rotação |
Engrenagens | Frequência de rotação Frequências de engrenamento e harmónicas Frequências de montagem Frequências naturais do sistema (defeitos das rodas dentadas da engrenagem) |
Turbinas de ventiladores e impulsores | Frequências da rotação Frequências de pás Harmónicas de frequências de pás e lâminas |
Rotores | Frequência de rotação Frequências naturais direcionais Harmónicas superiores |
Acoplamentos e cardans | Ordens da frequência de rotação |
Máquinas alternativas | Frequência de rotação e as suas ordens |
Na Tabela B, a seguir apresentada estão listadas características associadas a máquinas específicas. As frequências naturais e formas associadas aos modos de vibração do equipamento, podem fornecer informação útil durante o diagnóstico de um problema numa máquina. Esta informação é útil na previsão do desgaste, construção, corrosão, desaperto, alterações térmicas, e outros maus funcionamentos. As frequências naturais e modos de vibração são usualmente calculadas pelo fabricante ou utilizador.
Tabela B – Características de excitação e resposta da máquina
Tipo de máquina | Características |
Máquinas Centrífugas – Tipos de rotor | |
Bombas centrífugas | Chumaceiras rígidas Frequências de passagem de pás e seus múltiplos |
Compressores centrífugos | Grande razão entre peso da carcaça e peso do rotor Chumaceira de casquilho ou de almofadas Frequências de passagem de pás dos impulsores |
Ventiladores | Frequências de passagem de pás Aerodinâmica do sistema Características do pedestal frequentemente importantes |
Máquinas com Palhetas e Impulsores | |
Compressores de fluxo axial | Frequências de passagem de pás e seus múltiplos |
Turbinas de vapor ¾ acionamento mecânico | Frequências de passagem de pás 5000 RPM-12000 RPM gama para velocidades críticas Contactos e desequilíbrio de massa |
Turbina de vapor para geradores de energia | Frequências de passagem de pás Velocidade baixa – grandes carcaças Altas pressões Desequilíbrio de massa |
Turbinas de gás | Frequências de passagem de pás e de engrenagens Sujeito a instabilidades e contactos |
Equipamento de transmissão de potência | |
Engrenagens | frequência de engrenamento e harmónicas superiores ressonâncias da carcaça excitação pelos dentes das engrenagens das frequências naturais respostas torsionais |
Acionamentos hidráulicos | excitação da frequência de escorregamento instabilidade de pelicula de óleo |
Motores/Geradores | modulação da frequência de escorregamento vibração estrutural induzida por polos excitação induzida termicamente elevada excitação síncrono de motor no arranque curto-circuito no estator |
Máquinas alternativas | |
Acionamentos | Distorção da carcaça Vibração de fundação induzida pelas chumaceiras Excitação torsional por inércia e pressão |
Bombas e compressores | Excitação torsional por inércia e pressão |
Equipamento genérico | Avarias nos rolamentos Desaperto Problemas de correias e engrenagens |
Os detalhes de cada máquina deverão estar disponíveis antes da base de dados ser usada.
Atualmente, todos estes dados são registados nos programas de analise de vibrações que trabalham com os coletores de dados.
A lista de componentes mecânicos é crítica na estruturação da base de dados e para análise de acompanhamento. As especificações mínimas para motores elétricos incluem potência, velocidade de funcionamento, e informação específica acerca dos rolamentos; esta informação pode ser obtida usualmente da chapa de identificação ou do distribuidor. O tipo de motor (AC, DC, síncrono, de indução, alimentado por inversor) é usado para selecionar intervalos de medição e para fornecer informação analítica básica.
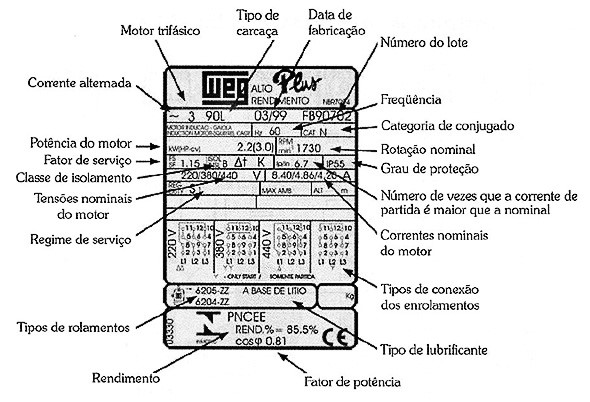
Informação específica sobre engrenagens redutoras é, normalmente, mais difícil de obter. A informação da chapa de identificação (modelo e número de série) fornece informação. Informação adicional, que inclui configurações internas e identificação de componentes de rolamentos e rodas dentadas, podem ser usualmente obtidas do fabricante. É sempre aconselhável solicitar um desenho da disposição geral que mostre a orientação dos componentes específicos.
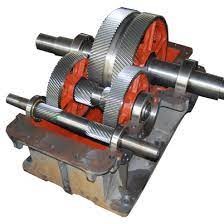
Outras máquinas que podem fazer parte de um programa de manutenção preditiva, são as bombas, máquinas ferramentas, misturadores de processo, trituradores, turbinas, e rolos de sucção. Dados mecânicos dos componentes incluem desenhos com a disposição geral, identificação dos rolamentos, velocidade de operação ou gama de velocidades de máquina, e tipo de acionamento. Quaisquer idiossincrasias relativamente à máquina – montagens, fraquezas óbvias e condições de processo que podem afetar o funcionamento e o diagnóstico – devem ser anotadas.
3.4 – Definição de avarias a detetar em cada máquina
Cada componente de uma máquina pode avariar-se de uma ou mais maneiras. Assim uma máquina pode avariar-se de múltiplas maneiras. Normalmente pretende-se detetar os seguintes tipos de avarias:
- As mais comuns
- As que põem em causa a segurança
- As com consequências mais onerosas em termos de custos, qualidade e ambiente
Se no caso das máquinas rotativas existem técnicas de controle fáceis de implementar, o mesmo já pode não se passar com outros tipos de equipamentos. Assim a facilidade com que se podem controlar uma determinada avaria é um fator a tomar em conta.
Sintoma Defeito | Temperatura | Pressão | Caudal | Vibrações |
Desequilíbrio | X | |||
Desalinhamento | X | X | ||
Rolamentos | X | X | ||
Desaperto | X | |||
Folgas | X |
Figura 1 – Avarias comuns e respetivos sintomas na implementação da monitorização de vibrações
3.5- Técnicas de inspeção
Parâmetros de medida
Os melhores parâmetros de medida que podem ser utilizados para fins do controlo de condição de uma máquina são aqueles cuja medição não interfira com o seu funcionamento.
Entre as técnicas de inspeção existentes, podem‑se referir por exemplo as seguintes:
- Medição de Vibrações
- Nível global
- vibraçoes de alta frequência nos rolamentos
- Espectro de frequência
- ‑ Controle de Desgaste
- Análise de óleos
- ‑ Controle de Desgaste
- Detetores de partículas
- Ferrografia
- ‑ Controle de Ruídos
- ‑ Controle de Fugas
Cada uma delas tem vantagens e defeitos, para além das suas limitações próprias. A sua aplicação implica, portanto, um conhecimento de todos os fatores em jogo, sendo comum aplicar‑se mais de uma técnica em cada máquina, quer como parâmetro para acompanhamento de uma tendência, quer para verificação da condição.
Quando se seleciona uma técnica de controlo para uma máquina critica, é importante notar que as máquinas se avariam porque uma ou mais componentes críticas falham.
Assim sendo, os métodos mais sensíveis de inspeção de uma máquina, funcionam através de deteção de sintomas de avaria em componentes individuais, visto o maior desvio das condições normais estar concentrado nesses sintomas tornando a anomalia mais fácil de detetar.
A seleção de um método de controlo depende assim do tipo de componentes mais suscetíveis de se avariar e do modo como isto ocorre. Podem‑se então considerar as hipóteses possíveis de controlar a degradação dessas componentes e poderá até ser possível encontrar uma só técnica que possa detetar todo o tipo de avarias prováveis numa máquina com uma eficácia razoável.
Por outro lado, a situação específica da manutenção de cada unidade industrial vai impor alguns constrangimentos na escolha das técnicas de inspeção a implementar.
No caso da avaria que se pretende controlar ter uma evolução muito rápida pode-se tornar necessário montar uma monitorização permanente. Caso este sistema tenha a capacidade de acionar um relé, designa-se então, por protetivo. É a chamada monitorização protetiva. Caso o objetivo da monitorização seja o de extrapolar, a partir do seu comportamento atual e do passado recente, o seu comportamento futuro, designa-se então por Monitorização Preditiva.
Que quantidade de parâmetros
Uma maneira de aumentar a fiabilidade de um sistema de controlo de condição reside em acompanhar múltiplos parâmetros e, por exemplo, realizar uma análise do espectro de frequência quando ocorre um alarme.
A desvantagem evidente deste sistema é a possibilidade de se ficar afogado em informação, mesmo assumindo que um computador e uma unidade de recolha de dados farão a maior parte do trabalho automaticamente. É duvidoso que toda essa informação adicional dê um grande contributo para o objetivo essencial do programa que é o de detetar avarias. Para começar, as rotinas de medição de vibrações colocarão o sistema bastante próximo dos seus objetivos principais no caso das máquinas rotativas.
3.6 -Equipamentos e sistemas de tratamento de informação na implementação da monitorização de vibrações
O principal objetivo da existência numa empresa de um determinado equipamento de controlo da condição é a deteção de avarias que se decidiu ser importante acompanhar. Assim o fator primordial na escolha de um equipamento consiste nas técnicas de deteção e diagnóstico de avarias que ele implementa. Existem, no entanto, outros fatores a tomar em conta que a seguir vão ser brevemente abordados.
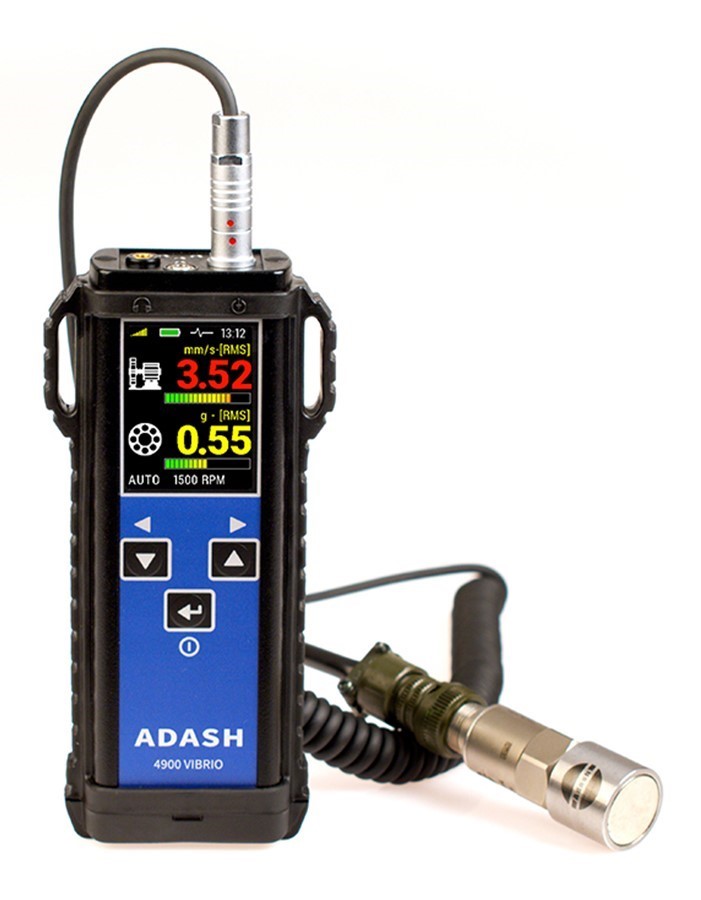
A seleção do equipamento de medida depende do funcionamento do programa, do número de pontos de medida e da profundidade da análise pretendida.
Se o equipamento de medida foi adquirido antes de o programa ter sido planeado, pode ter de ser adaptado para o equipamento existente nas instalações fabris. De outra forma, o equipamento e o software podem ser escolhidos de modo a ir ao encontro das necessidades do programa. Se houver dúvidas acerca do equipamento de medida apropriado, escolha instrumentos que sejam versáteis e de confiança. No mínimo, o coletor de dados e o software deverão ser capazes:
- Prever a tendência de leituras globais e de banda;
- Medidas em deslocamento, velocidade e aceleração;
- Medições de níveis rms, pico e pico-pico;
- Executar integração analógica e/ou digital;
- Medições HFD globais (aceleração filtrada em alta frequência);
- Providenciar espetros com pelo menos até 6400 linhas de resolução;
- Espectro de alta frequência desmodulado (envelope) com filtros selecionados.
- Forma de onda;
- Gama dinâmica de 120 dB;
- Janelas Hanning ou Uniforme;
3.6.1 ‑ Tendência e diagnóstico na implementação da monitorização de vibrações
Quando se faz implementação da monitorização de vibrações nas máquinas podem‑se definir diversas fases.
Quando o sistema está a funcionar o seu objetivo imediato é detetar avarias. Numa determinada máquina, em boas condições de funcionamento, está‑se no período de deteção de avarias. Quando os níveis começam a subir vai‑se elaborar uma tendência para tentar avaliar quando é necessário parar a máquina e ao mesmo tempo vai‑se fazer um diagnóstico. Definem‑se assim mais duas fases: a de elaboração da tendência e a de diagnóstico.
Para auxiliar o diagnóstico é frequente fazer a “assinatura” da máquina quando ela se encontra em boas condições de funcionamento. A “assinatura” consiste em espectros de frequência, obtidos em um ou mais pontos da máquina que servirão de base de comparação para quando ocorrem anomalias.
Surge assim a necessidade de existirem equipamentos para detetar e diagnosticar as avarias. A função de deteção ocupa a primeira prioridade e a de diagnóstico a segunda.
Torna‑se também evidente que a quantidade de informação gerada em todo este processo é muito elevada, podendo ser importante o recurso a um computador para a tratar, podendo, por exemplo, a função tendência ser por ele executada.
3.6.2 – A informatização da implementação da monitorização de vibrações
Quando se controla um numeroso grupo de máquinas, dezenas ou mesmo centenas, a questão do tratamento da informação obtida e do custo desse tratamento começa‑se a pôr com alguma premência podendo‑se impor então o recurso a um suporte informático. O suporte informático neste contexto apresenta as seguintes vantagens:
- Automatização do processo
- Organização da informação
- Aumenta a precisão
- Poupa tempo
- Aumenta o tempo de pré-aviso
- Permite melhor planeamento
Os resultados são maior capacidade com menor custo:
– Podem-se controlar mais máquinas
– Podem-se controlar mais pontos críticos
– O controle tem maior eficácia económica
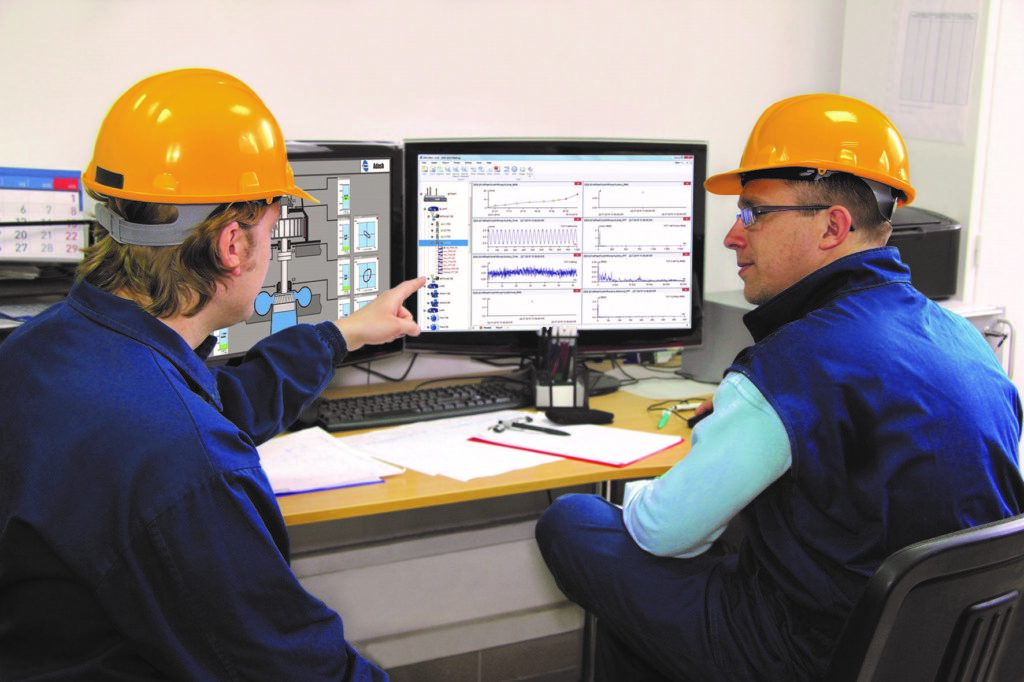
3.7 -Procedimentos de medida
Quando os resultados de medida de um determinado parâmetro forem significativamente influenciados pela maneira como ela é executada, há que elaborar um procedimento de medida. Como é evidente é este o caso das vibrações.
Normalmente no procedimento de medição de vibrações está incluída a definição dos seguintes parâmetros:
- Esquema da máquina
- Localização dos pontos de medida
- Medida a efetuar
- Parâmetros da medida
- Fixação do sensor
- Equipamento de medida
Hoje em dia, a informação contida nos procedimentos tende a estar contida no programa de manutenção preditiva, no computador, não existindo, portanto, documentos com esse nome.
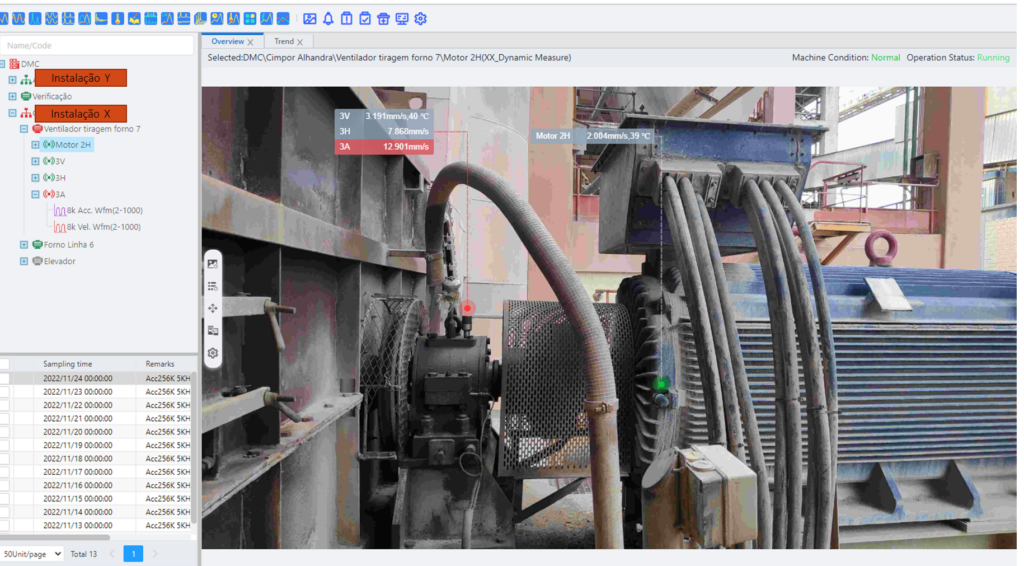
3.8 Triagem
A triagem é usada para avaliar, a um custo relativamente baixo, quando um problema se está a desenvolver-se numa máquina específica.
Permite ganhar tempo para uma análise e para preparar para reparação. As técnicas de triagem variam em sofisticação e eficácia. A eficácia depende do aparelho usado e do tipo de máquina monitorizada. Devem ser dadas permissões para alterações nas condições de funcionamento que afetam os níveis de vibração global. Tais mudanças podem ser causadas por alterações no processo ou condições ambientais. Qualquer mecanismo que possa ser usado para relacionar alterações na vibração devidas a alterações no processo aumenta a eficácia de um programa. As tendências deverão, se possível, basear-se somente nas alterações da condição da máquina. É assim uma boa política de monitorização, implementar uma ampla análise de vibração antes de iniciar uma ação de manutenção.
Triagem com medição de nível global de vibrações
Os aparelhos de triagem incluíam chaves de parafusos, fios e estetoscópios. Eram usados para detetar avarias em rolamentos.
Um aparelho de triagem como um medidor de rms verdadeiro e um acelerómetro é simples, mas implica trabalho intensivo.
O valor rms pode ser calculado por um analisador FFT com dados recolhidos a partir de um transdutor de velocidade ou um acelerómetro, dependendo da máquina. Uma duplicação do nível de vibração usualmente indica que é necessário fazer alguma ação, ou uma análise de vibração mais detalhada ou iniciação da reparação.
Triagem com medição simples de defeitos em rolamentos
Outros instrumentos simples — por exemplo, medidores de defeito de alta frequência e valor único para identificar avarias em rolamentos — usam a resposta de acelerómetros a impulsos resultantes de uma avaria num componente específico da máquina. A resposta do acelerómetro é filtrada de modo a incluir somente a atividade em redor da sua frequência natural.
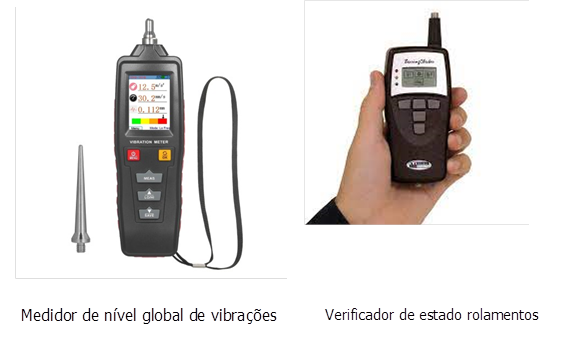
Os medidores de defeitos em rolamentos simples, são aparelhos adequados para triagem se no ponto de medição não estiverem presentes outros impulsos e ruído. Por exemplo, as alterações no nível de vibração que ocorrem quando uma avaria acontece num ventilador bem equilibrado acionado por um motor com uma frequência de passagem de palhetas baixa, serão detetadas porque podem ser sentidos impulsos associados com rolamentos. No entanto, um instrumento indicador de impulsos pode não ser capaz de distinguir uma nova falha se o nível do impulso da falha for baixo em relação à vibração da frequência de engrenamento da máquina.
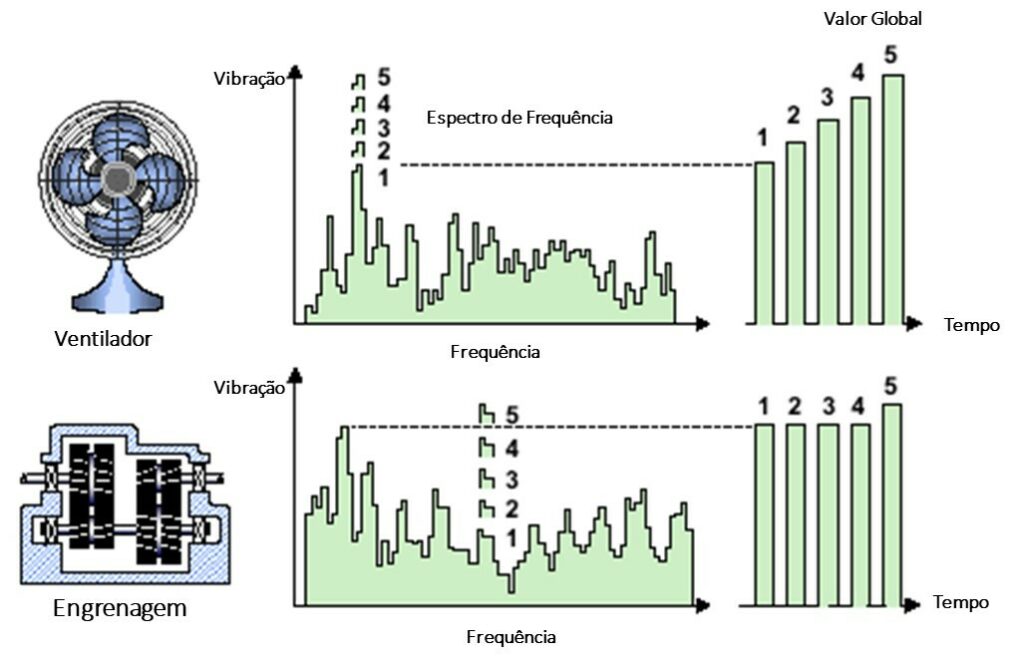
Figura – A sensibilidade de medições globais em espetros complexos
Uma falha de um mecanismo que está a causar sinais de baixa velocidade ou aceleração a partir de um acelerómetro pode estar disfarçado por uma frequência normal de outro componente. Um espectro de uma caixa de engrenagens na qual o engrenamento encobriu uma falha num rolamento é mostrado na figura a seguir.
Os níveis globais de impulsos e vibração não se alteraram quando o rolamento avariou, mas a análise do espectro mostrava que uma avaria no rolamento era iminente. Portanto quando ruído aleatório e vibração estão presentes, métodos de triagem simples podem não ser eficazes, especialmente aqueles que dependem de impulsos.
Métodos mais avançados de monitorização de vibrações
Um nível mais sofisticado de triagem envolve filtragem de bandas; isto é, mostrar alterações na vibração em bandas distintas de frequência.
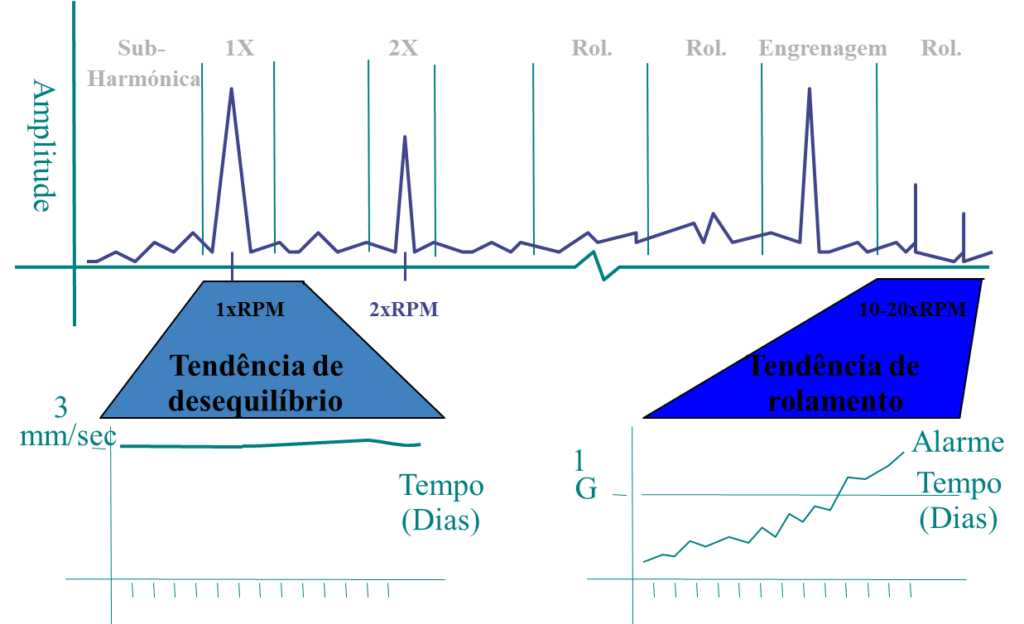
O espectro mostrado na figura anterior foi dividido em bandas de frequência que separa as falhas de desequilíbrio ou desalinhamento (1x, 2x, 3x e 4x), frequências de rolamento, e frequências de engrenamento. Assim, alterações de níveis globais indicadas por uma única leitura de velocidade não indicaram uma iminente avaria do rolamento, mas os resultados filtrados sim. Num coletor de dados podem ser parametrizadas gamas de frequência distintas.
A triagem de amplitude do nível global de vibrações em velocidade eficaz é frequentemente malsucedida, na deteção de defeitos nos rolamentos. O espectro e a forma de onda devem ser usados para estudar as frequências e a energia. A situação pode ter sucesso ao monitorizar alguns rolamentos em máquinas de baixa velocidade. O pico de vibração obtido de uma forma de onda ou de um circuito de deteção de pico pode ser mais sensível à condição do rolamento do que as medições espectrais.
A figura a seguir contém um espetro medido nas chumaceiras de motor de um ventilador em que as turbinas estavam montadas no veio do motor. Neste espetro a amplitude da componente vibratória da frequência a passagem de pás, a 395 Hz é muito maior que as amplitudes das harmónicas de 100 Hz indicadoras de um problema elétrico no motor.
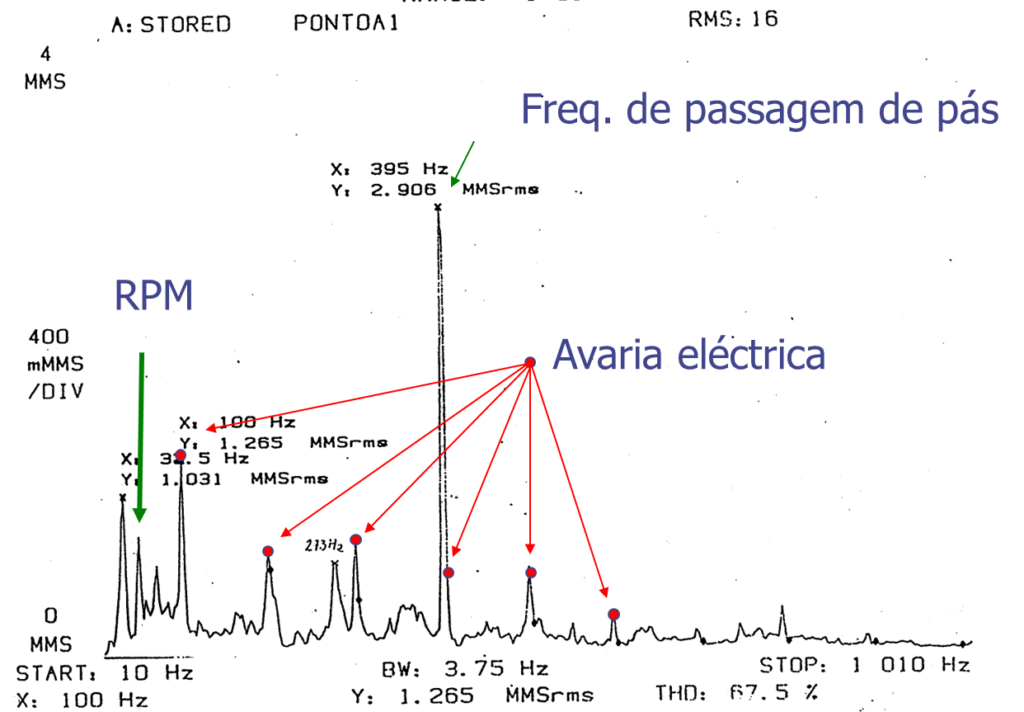
Figura – Espetro medido nas chumaceiras de motor de um ventilador em que as turbinas estavam montadas no veio do motor
Este é um exemplo em que a medição do nível global de vibrações e incapaz de identificar os sintomas vibratórios existentes de anomalia elétrica no motor.
Em alguns casos de máquinas de alta velocidade (3600 RPM e superior) as avarias nos rolamentos ocorrem rapidamente e defeitos na gama de frequência do rolamento, criam níveis de vibração muito baixos. Os defeitos do rolamento podem surgir mais distintamente na gama de alta frequência (5 kHz to 40 kHz) do espectro. Estas respostas de alta frequência são tipicamente frequências naturais excitadas pelos defeitos nos rolamentos.
Métodos baseados no envelope funcionam bem nestes casos e, por isso, hoje em dia são muito utilizados. As vibrações de baixa frequência à velocidade de funcionamento e as vibrações induzidas pelo engrenamento são filtradas para fora do sinal; caso contrário, as suas amplitudes mais altas criam um problema de intervalo de variação dinâmico. O sinal filtrado é desmodulado para produzir um sinal livre de frequências naturais. Um espectro do sinal desmodulado mostrará as frequências do rolamento e a natureza da avaria.
3.9 -Avaliação do resultado das medidas
A maneira simples e eficaz de estabelecer critérios de avaliação para as vibrações das máquinas é através do seu histórico. Uma regra simples é a seguinte: quando a amplitude da vibração duplica, existe um problema; quando a amplitude da vibração triplica a máquina tem que ser posta fora de serviço para uma intervenção de manutenção.
Não existem disponíveis valores, prontos a usar, para toda e qualquer máquina. A maioria dos fabricantes das máquinas têm um limite de vibrações para as suas máquinas, no entanto existindo uma enorme quantidade de variáveis que influenciam os níveis vibratórios de uma máquina instalada, torna-se impossível aplicar realisticamente os mesmos critérios em controle de qualidade e manutenção.
A analise de tendência
A analise de tendência e a melhor abordagem para definir qual deve ser o limite de vibração para uma máquina.
Assim o que é sugerido é que, numa fase inicial do arranque do sistema, não se tente logo estabelecer conclusões sobre o estado da máquina a partir das primeiras medições. Os primeiros resultados servirão essencialmente para começar a definir critérios de avaliação realistas.
De qualquer modo na normalização ISO encontram-se definidos muitos limites de vibrações em máquinas.
Aquando da realização das primeiras medidas numa máquina, se não existir nenhum problema, as vibrações vão ser de amplitude reduzida. Caso se meçam vibrações de amplitude elevada tem de se olhar com atenção para a máquina e verificar se não existe nenhuma causa relacionada com o seu princípio de funcionamento ou montagem que lhes dê origem. Caso não exista é possível que exista verdadeiramente um problema na máquina. Para verificar se este é o caso há que averiguar o seu histórico.
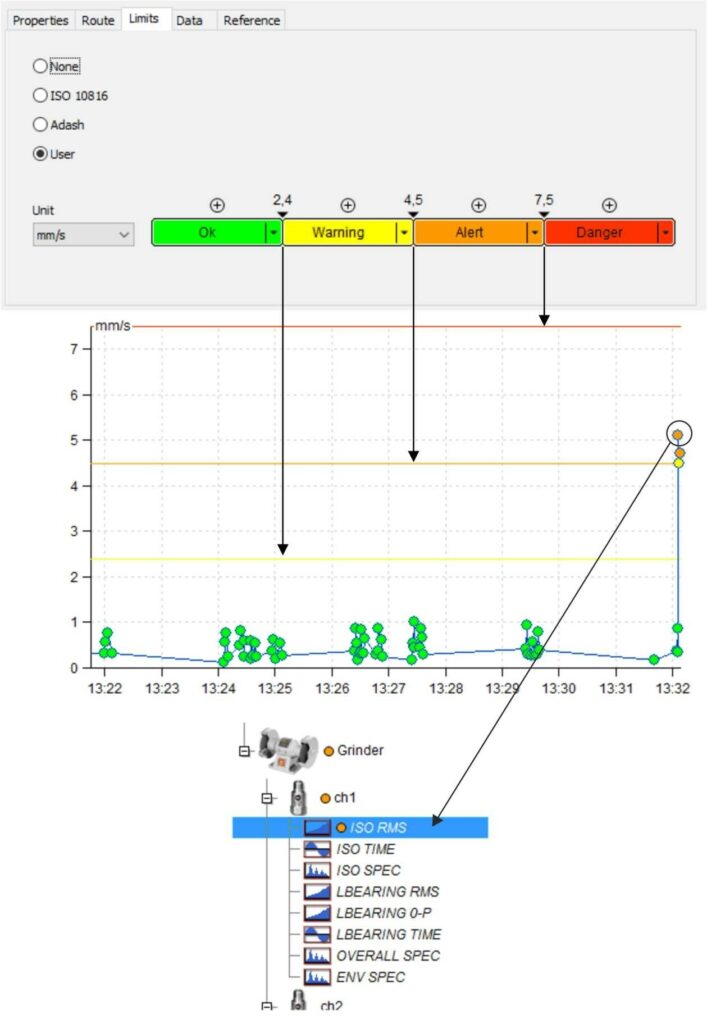
3.10 -Periodicidade das medidas na implementação da monitorização de vibrações
O objetivo da realização de medições periódicas é detetar os problemas nas fases iniciais. O intervalo entre medidas deve ser suficientemente curto para fornecer uma garantia razoável que se vai detetar o surgimento de um problema e acompanhar a sua evolução. Por outro lado, é antieconómico realizar inspeções com excessiva frequência.
De um ponto de vista teórico o que dita o intervalo entre medições é o tempo médio entre avarias. Para o sistema ter uma fiabilidade razoável têm de se realizar no mínimo seis medições no referido período.
Na prática o intervalo entre medidas é função de diversos parâmetros:
- – Importância da máquina
- – Historial da máquina
- – Técnica de controle
- – Condição da máquina
- – Tempo médio entre avarias
- – Regime de funcionamento
- – Disponibilidade de pessoal
Máquinas que estão a dar problemas ou equipamentos muito grandes, de alta velocidade, poderão ter que ser controlados numa base diária. Outras máquinas poderão ser controladas numa base quinzenal ou mensal. A disponibilidade de pessoal para realizar estas inspeções também será sempre um fator importante para decidir sobre o intervalo entre as inspeções.
Em qualquer caso o melhor indicador para selecionar o intervalo para verificações periódicas é o histórico da máquina. Se as avarias tiverem sido frequentes serão necessárias verificações frequentes. Em caso de dúvida sobre o intervalo adequado para as inspeções numa determinada máquina, poder‑se‑ão fazer inicialmente inspeções com uma frequência elevada, sendo o período entre inspeções posteriormente alargado, ou não, em função da experiência.
3.11 -O planeamento da monitorização de vibrações
Como já foi múltiplas vezes referido o sistema de controle de condição baseia‑se na execução de inspeções regulares às máquinas. Para isto poder ter lugar é necessário elaborar um planeamento das inspeções. Com este planeamento vai‑se assegurar que as inspeções vão ter lugar nos intervalos previstos e que a carga de trabalho vai ser equilibrada. A base do planeamento é a organização de percursos de inspeção (rotas).
Um percurso de inspeção constitui um grupo de máquinas, com igual periodicidade de inspeção.
Existem duas abordagens distintas para a criação de percursos de inspeção:
a) No mesmo percurso, as máquinas estão localizadas na proximidade uma das outras. Esta aproximação tem a vantagem de minimizar o tempo de deslocação entre as máquinas.
b) No mesmo percurso as máquinas estão distribuídas pelas diversas áreas fabris. Neste caso a vantagem reside em existir a possibilidade de se fazer controlo sensorial, em grande parte das instalações, durante a deslocação de máquina para máquina.
A primeira abordagem é mais utilizada quando existe disponibilidade de pessoal para implementar intervalos entre inspeções razoavelmente curtos. Quando isto não é possível, a segunda abordagem apresenta a vantagem de assegurar uma vigilância mínima num grande número de equipamentos.
Para definir um percurso procede-se da seguinte forma:
- Listar as máquinas de acordo com a sua localização.
- Listar a periodicidade de inspeção por máquina.
- Listar o número de medidas por máquina.
- Ver o número de medidas por percurso.
- Agrupar as máquinas em percursos.
- Definir a sequência de inspeção em cada percurso.
Por fim com os percursos de inspeção já definidos elabora‑se um Planeamento de todos os percursos a executar.
4 -FORMAÇÃO E SENSIBILIZAÇÃO PARA A IMPLEMENTAÇÃO DE UM SISTEMA DE MONITORIZAÇÃO DE VIBRAÇÕES
Aspeto muito importante para o sucesso do sistema de controle de condição é o da formação do inspetor. Se há efetivamente algumas ações de inspeção para as quais não é preciso formação particular, outras há, como seja por exemplo as vibrações, para as quais convém que seja dada uma formação específica. Aspeto também da maior importância é o da sensibilização das chefias diretas. É frequente encontrar situações em que existam pessoas, com responsabilidade na estrutura da manutenção, que recusam a informação dada pela inspeção por não terem capacidade para a compreender e/ou estarem desmotivadas para o fazer.

Normalmente o pessoal que já trabalha na manutenção pode ser aproveitado para efetuar as inspeções. A sua experiência anterior ajudá-lo-á a diagnosticar avarias e fazer o controlo sensorial.
4.1 – O inspetor na implementação da monitorização de vibrações
O inspetor é um elemento fundamental do sistema de monitorização de vibrações. Dependendo das funções que lhe são atribuídas assim existirão diferentes requisitos para a sua qualificação. Qualquer que seja a opção, tem que existir especial cuidado com a sua motivação. A ação de inspeção, por si só, pode tornar-se uma tarefa muito monótona e sua desmotivação pode deitar abaixo os objetivos do plano de manutenção preditiva. Assim ter-se-á:
Com qualificação – Analista de Vibrações Nível I
- Funções – Inspeção
- Diagnóstico muito básico
- Elaboração de Relatórios
- Desvantagens desta opção
- Fácil desmotivação
- Limitação ao desenvolvimento do sistema
- Os procedimentos de medida têm de ser rigorosamente exatos
- Diálogo dificultado com outros interlocutores na organização fabril
Técnico com qualificação Analista de Vibrações Nível II
- Funções – Inspeção
- Diagnóstico
- Elaboração de relatórios
- Elaboração de pedidos de trabalho
- Acompanhamento de reparações
- Controle do trabalho de terceiros
- Vantagens
- Maior facilidade de motivação
- O sistema de controle de condição evolui com maior facilidade
- Diálogo facilitado com interlocutores na organização fabril
4.2 – A função das chefias diretas e gestores da manutenção na implementação da monitorização de vibrações
A correta motivação das chefias diretas da manutenção é da maior importância para o sucesso da implementação da monitorização de vibrações. Em casos extremos a sua desmotivação pode levar a ações do tipo sabotagem.
Especialmente em unidades industriais a funcionar há bastantes anos, existe a tendência de encarar a implementação de um sistema de inspeção, como uma prova de desconfiança. Nestas circunstâncias, o trabalho da inspeção não só é recusado como também chega a ser sabotado. Assim é da maior importância que as chefias diretas da manutenção sintam a manutenção condicionada como algo que é feito com elas e não contra elas. Para este fim há que envolvê-las desde os primeiros momentos na implementação do sistema de inspeção. É também extremamente importante que compreendam a informação que lhes é fornecida pela inspeção. Assim também se torna necessário que frequentem ações de formação na área da monitorização de vibrações.
Também não se pode esquecer o papel fundamental para o diagnóstico das avarias que existe nestas funções. Frequentemente só se consegue compreender o que aconteceu ou está a acontecer nas máquinas com a sua colaboração.
Como é evidente parte do que se disse é aplicável a todos os gestores da manutenção surgindo assim necessidades de sensibilização/formação paralelas.
4.3 – Produção
Atualmente existe a perspetiva de encarar a produção, como um cliente da manutenção, com quem tudo deverá ser negociado, incluindo como é obvio as paragens para efeito de manutenção. Caso seja este o caso também existirá a necessidade de os gestores da produção compreenderem as vantagens e limitações do controle da implementação da monitorização de vibrações.
5 -RAZÕES PARA A IMPLEMENTAÇÃO DE UM SISTEMA DE MONITORIZAÇÃO DE VIBRAÇÕES FALHAR
Existem duas ordens de razões diferentes que podem levar um sistema a falhar:
– Razões de ordem técnica
– Problemas de gestão
5.1 – Razões de ordem técnica
Os problemas de ordem técnica que normalmente ocorrem são:
– Falsos alarmes
– Avarias não detetadas
Os falsos alarmes resultam, na maioria das vezes, de critérios de avaliação mal definidos, daí a ênfase que se dá à sua constituição a partir do histórico das medidas.
Na fase inicial da implementação do sistema há que ter extremo cuidado com a emissão de alarmes. Efetivamente não há nada que lance um maior descrédito ao sistema que se constatar que uma máquina, intervencionada na sequência da emissão de um alarme pela inspeção, efetivamente, não tem nada de anormal.
Tem de se ter sempre presente que a fase inicial de lançamento de um sistema de monitorização de vibrações é uma fase crítica de diversos pontos de vista:
– As pessoas envolvidas normalmente ainda não têm muita experiência
– Ainda não existe um histórico das máquinas
– Existe uma grande expectativa em relação ao sistema
Assim não só as possibilidades de emitir pareceres incorretos são elevadas, mas também as consequências são graves, no mínimo, a nível de credibilidade do sistema.
As avarias não detetadas resultam frequentemente de leituras e procedimentos incorretos.
Constata-se a existência de muitas situações em que as empresas começam por comprar um “Medidor de Vibrações” (?), o que quer que isto seja, começando de seguida a fazer medidas. Como previamente não se averiguou o que se estava efetivamente a controlar, começam a surgir as surpresas…
5.2 -Problemas de gestão
A este nível os problemas podem ser múltiplos e vai-se apenas referir alguns.
– Desconfiança inicial
Na fase inicial de lançamento do sistema de monitorização de vibrações existe normalmente, da parte de muitas pessoas, desconfiança em relação ao mesmo. Convém assim que, após a resolução dos primeiros casos práticos, se faça internamente uma divulgação alargada – mesmo junto dos níveis hierárquicos mais elevados na empresa – dos resultados obtidos. Com esta acção pretende-se aumentar a credibilidade do sistema, melhorar o relacionamento entre as pessoas, criar atitudes construtivas perante os problemas e reforçar o espirito de equipa.
– Desmotivação do Inspetor
Como já foi referido o trabalho de inspeção pode-se tornar, quando feito isoladamente, bastante monótono. Assim convém atribuir ao inspetor outras funções para além da inspeção e fazer-lhe compreender e sentir claramente a importância e responsabilidade que a sua tarefa tem para uma eficaz gestão da manutenção.
– Desmotivação da Produção e da Gestão em geral
Mesmo que numa fase inicial o sistema tenha sido bem-sucedido, ocorrem situações em que com o passar do tempo o sistema “cai”. Isto acontece porque não existia um sistema claro de seguimento dos sucessos do sistema de monitorização de vibrações por parte da gestão. É assim absolutamente necessário que seja montado um sistema de relatórios regulares (trimestral por exemplo) da atividade da inspeção onde se assinalem as avarias detetadas, prejuízos evitados, etc, com estimativas dos ganhos obtidos. É também conveniente que sejam definidos objetivos anuais, ações corretivas e métodos de acompanhamento do sistema.
6 A FUNÇÃO DA INTELIGÊNCIA ARTIFICIAL
Atualmente até os medidores mais simples tem alguma forma de inteligência artificial a apoiar o diagnóstico por analise de vibrações.
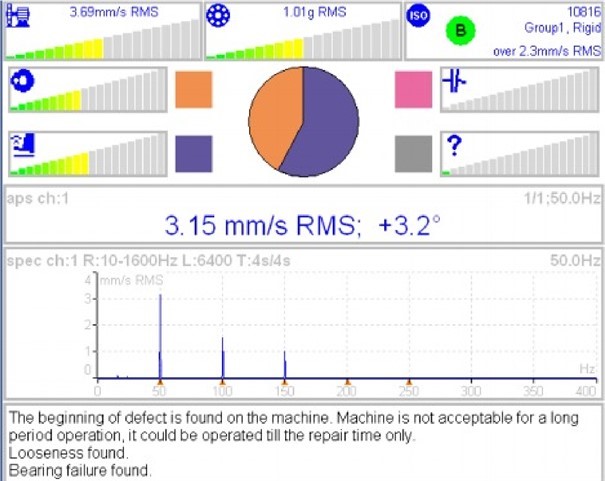
Quanto mais simples for a máquina, melhor funcionam. Todavia, com a tecnologia atual, não conseguem substituir um analista certificado.
Quem tomar decisões de manutenção, só baseadas no que estes sistemas dizem, vai passar por más experiências …
Devem ser encarados como uma ajuda na interpretação dos resultados das medidas; foi para isso que foram concebidos.