Instrumentación de supervisión de turbinas
1 introducción – Instrumentación de supervisión de turbinas (ETI)
Este artículo presenta la instrumentación de supervisión de turbinas..
Este artículo pertenece a una serie., el cual constituye el material de apoyo para el curso de análisis de vibraciones en turbomaquinaria. Los enlaces a los otros artículos se pueden encontrar aquí.
La transición de vapor a gas
En tiempos, la mayor parte de la producción mundial de electricidad provino de turbinas de vapor acopladas a generadores. Si el vapor se produjo quemando combustibles fósiles convencionales, como el carbón, gasolina o aceite, ya sea por el calor de la fisión nuclear en un reactor, el proceso fue esencialmente el mismo: calentar agua a vapor, expandirlo a través de una turbina acoplada a un generador y reciclar el vapor/agua agotado para calentarlo nuevamente a través de la caldera o reactor.
En este momento, los métodos de producción para satisfacer la demanda mundial de energía se han desplazado en gran medida a las turbinas de gas en lugar de las turbinas de vapor, aumentada por un porcentaje mucho mayor de fuentes renovables (viento, solar, geotérmica).
Este cambio se produjo por dos motivos.: Las turbinas de gas son más eficientes que las turbinas de vapor para extraer energía de una cantidad dada de combustible, y las turbinas de gas generan menos contaminantes. (emisiones por MW de producción).
Las turbinas de gas más eficientes del mundo, por ejemplo, actualmente puede alcanzar eficiencias cercanas a 45%. En comparación, plantas compuestas únicamente de turbinas de vapor rara vez superan el 35% de eficiencia.
La persistencia de las turbinas de vapor
De cualquier manera, todavía hay una base instalada considerable de turbinas de vapor en todo el mundo y seguirá existiendo en el futuro previsible. Además, continuará la instalación de nuevas turbinas de vapor, ya que el calor residual de los gases de escape de una turbina de gas se puede utilizar para hervir agua y crear vapor para una turbina de vapor. Estas centrales eléctricas se conocen como “ciclo combinado” porque combinan los ciclos termodinámicos de las turbinas de gas y vapor en la producción de electricidad. consecuentemente, son más eficientes que las llamadas centrales de “ciclo simples” – si consisten solo en turbinas de gas (eficiencia típica de 35-40%) o simplemente por turbinas de vapor (eficiencia típica de 30-35%).
En contrapartida, una planta típica de ciclo combinado tiene una eficiencia de 50-60%. Esta mayor eficiencia se debe al hecho de que el calor de la turbina de gas, que antes subía por la chimenea de escape, ser enrutado a través de un HRSG (Generador de vapor de recuperación de calor).
El vapor resultante se expande a través de una turbina que impulsa otro generador eléctrico., producir más energía sin necesidad de ningún combustible adicional. Un contenido de combustible idéntico en una planta de ciclo combinado produce, así, más MW de electricidad que una planta de energía de turbina de gas de ciclo único de tamaño similar.
el tamaño es importante
Una de las formas de optimizar la eficiencia de las turbinas de vapor es a través del tamaño.. Una turbina de vapor grande es más eficiente que varias turbinas de vapor pequeñas que funcionan en paralelo para producir energía equivalente.. En una planta de energía alimentada por combustibles fósiles, una turbina de vapor típica tiene dimensiones que van desde 50 MW e 1200 MW (Figura 1.1). numa central nuclear, una turbina de vapor típica tiene una dimensión que varía entre 800 MW e 1770 MW. El enorme tamaño de estas máquinas hace que los rotores sean a menudo muy largos.. Además, cómo se diseña el recinto de una turbina de vapor como un recipiente a presión, suele ser muy grueso (300 milímetro o más) y se expande/contrae más lentamente que el rotor. Estos y otros factores se combinan para dar como resultado un conjunto de mediciones que son exclusivas de los grandes generadores de turbinas de vapor y complementan la vibración radial convencional., la referencia de fase, Mediciones de temperatura y posición axial de rodamientos típicas de todas las máquinas rotativas con rodamientos de película fluida..
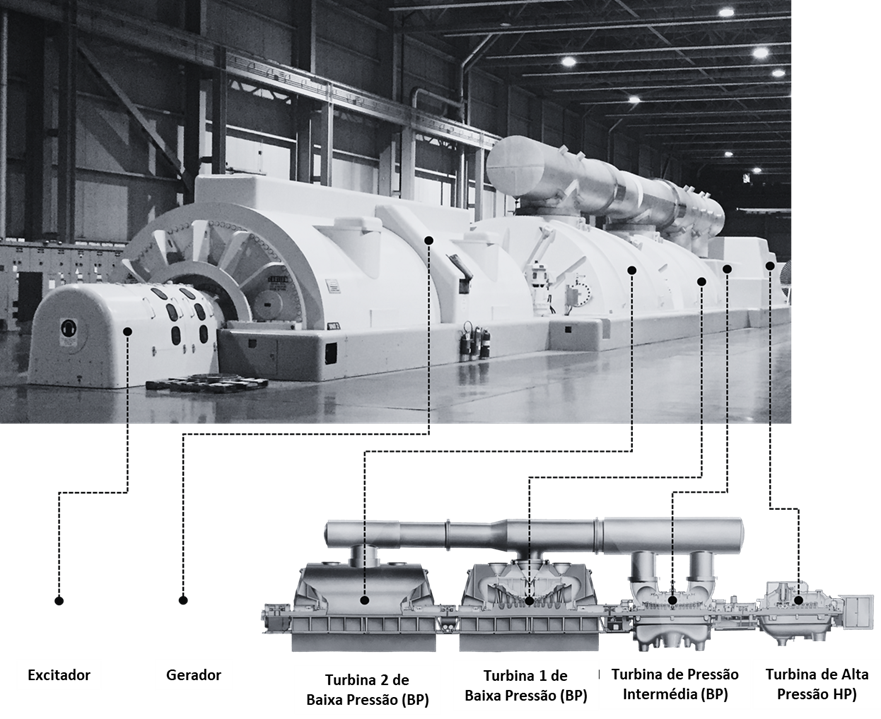
Instrumentación de supervisión de turbinas – Figura 1.1 Un generador de turbina de vapor de 525MW compuesto por cuerpos de Alta Presión (punto de acceso), Presión intermedia (Pi) y presión arterial baja) (dos), junto con generador y excitador. El vapor entra en la caja de la turbina de alta presión por la parte inferior y sale por la parte superior., donde fluye a las dos turbinas de Baja Presión paralelas.
2 Instrumentación de supervisión de turbinas – mediciones especializadas
Las mediciones especializadas exclusivas de los generadores de turbinas de vapor se realizan con la llamada instrumentación de monitoreo de turbinas. (ETI) y se describen a continuación. Estas medidas, junto con mediciones de vibraciones convencionales, posición, referencia de temperatura y fase, se muestran en la figura. 2.
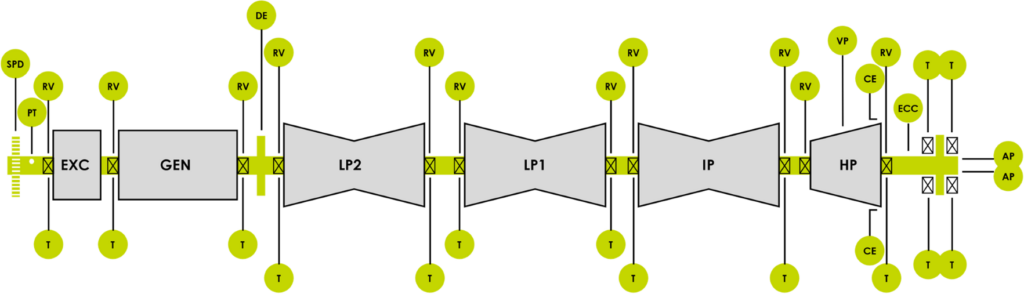
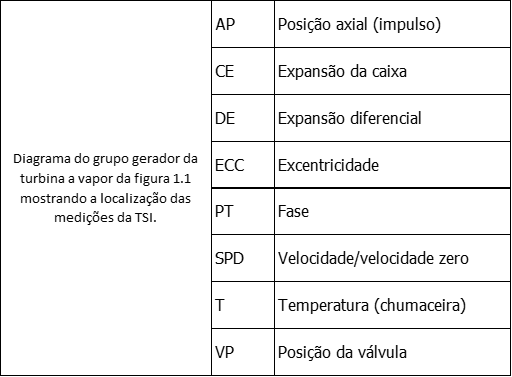
Instrumentación de supervisión de turbinas – Figura 1.2 – Diagrama del grupo electrógeno de turbina de vapor 1.1 mostrando la ubicación de las mediciones TSI
Expansión diferencial (DE)
Tal como referido anteriormente, grandes turbinas de vapor tienen carcasas masivas, con respecto a su rotor, lo que resulta en diferentes tasas de expansión térmica. Esto es debido, en parte, diferencias en metalurgia y coeficientes de expansión térmica correspondientes, sino también a las extremas diferencias de masa e inercia térmica entre el rotor (relativamente) ligero y su carcasa mucho más pesada.
Cuando se introduce vapor sobrecalentado en una turbina, sus carcasas y rotores se expanden a diferentes velocidades. Si la expansión de estas partes entre sí no se mide y controla rigurosamente, las partes giratorias (por ejemplo, las palas de la turbina) puede entrar en contacto con piezas no giratorias (diafragmas de turbina) y pueden ocurrir daños sustanciales..
Para maximizar la eficiencia de las turbinas de vapor, Las holguras entre las hojas y los diafragmas son – por proyecto – bastante apretado y solo se puede tolerar una pequeña cantidad de movimiento diferencial.
Las mediciones de expansión diferencial a menudo se toman cerca de la carcasa de baja presión porque el eje está limitado axialmente en la ubicación del cojinete de empuje. (cerca de la turbina de alta presión) y luego crece (expandir) hacia afuera desde ese punto a lo largo de la longitud de la máquina a través de los marcos PI y BP.
Sin embargo, la ubicación puede variar según la carcasa de la turbina que se esté midiendo para determinar la expansión diferencial. Por ejemplo, la maquina de figuras 1.1 tiene medición de expansión diferencial en el lado externo de la turbina AP, como se muestra en la figura 1.2. Independientemente de dónde se encuentre el sitio de medición de ED, El principio es el mismo: comprobar el crecimiento térmico relativo entre el marco de la turbina y el rotor.
Como la cantidad de expansión térmica puede ser sustancial, y más allá del rango lineal de la mayoría de las sondas de proximidad convencionales, a menudo es necesario utilizar una disposición especial de dos sondas para cubrir todo el rango de expansión diferencial.
Sin embargo, en algunos casos, solo un solo transductor puede abordar el rango requerido – particularmente cuando se usan los llamados sensores de presión. “gama alargada”. Cada tipo de medición de expansión diferencial se describe a continuación..
Expansión diferencial de un solo canal (Pegar) SCDEC
Esta medida se realiza con una sola sonda de proximidad, fijado a la caja de la máquina, y observando un collar especial diseñado específicamente para la medición DE (Figura 2). El espacio entre la punta de la sonda y la superficie perpendicular del collar observado representa el movimiento relativo entre la carcasa y el rotor..
Nota: Cuando la sonda está rígidamente unida a la base de la máquina, en lugar de la caja de la máquina, la contribución debido a la expansión de la caja se elimina de la medición. Esto se conoce como expansión del rotor., ya que indica la cantidad de crecimiento/contracción absoluta del rotor solamente, en lugar de su relación con la caja, que también puede crecer/encogerse.
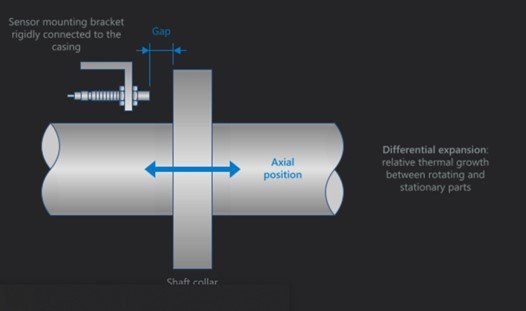
Instrumentación de supervisión de turbinas – Figura 2 Captura de pantalla del software de configuración VM600MK2 (PROTECCIÓN VibroSight) que representa una medida de expansión diferencial de un solo canal (Pegar).
Expansión diferencial de un solo canal (péndulo) SCDEP
Esta medición se realiza utilizando un péndulo especial que cambia el ángulo del objetivo de la sonda a medida que el eje se expande o se contrae en relación con la carcasa de la máquina..
El ángulo cambia a través de un imán en el collar del eje que tira del péndulo en cualquier dirección a medida que el eje crece o se encoge.. Uso de las relaciones trigonométricas entre las diversas geometrías de la matriz de sonda/objetivo, los cambios en la apertura de la sonda se convierten en expansión diferencial real. De esta forma, se puede observar un rango de expansión mucho más amplio que si la nave espacial estuviera simplemente observando un collar perpendicular. Ver Figura 3.

Instrumentación de supervisión de turbinas – Figura 3 – Captura de pantalla del software de configuración VM600Mk2 (PROTECCIÓN VibroSight) representando una medida SCDEP. en la imagen inferior, el eje se ha expandido a la izquierda, girando el péndulo en el sentido de las agujas del reloj y aumentando el espacio de la sonda (Espacio 2 > Espacio 1).
Expansión diferencial de doble canal (pegar) DCDEC
Esta medición utiliza dos sondas: uno frente al otro y mirando a lados opuestos del collar DE.
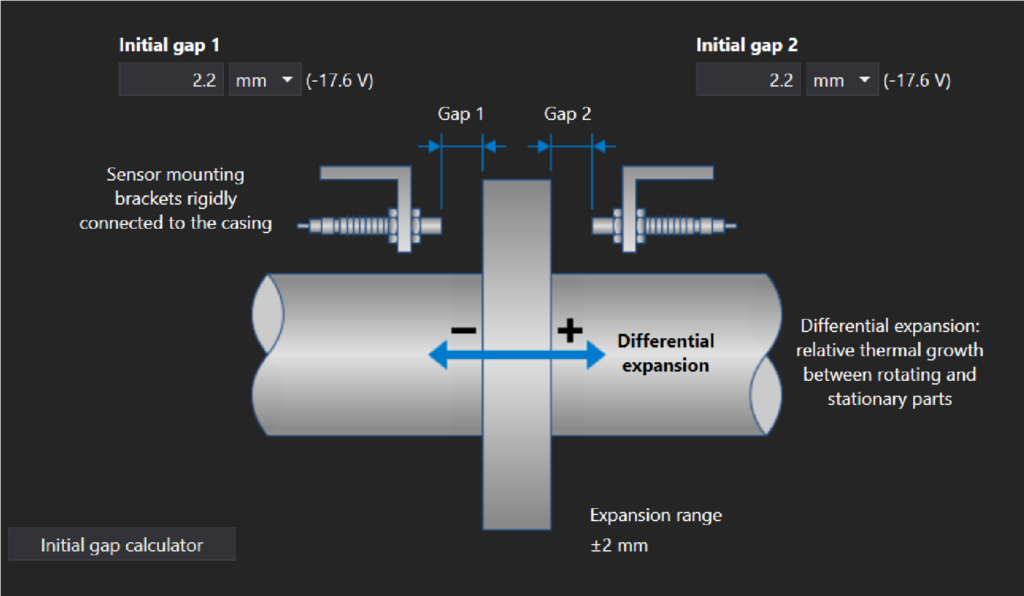
Instrumentación de supervisión de turbinas – Figura 4 – Captura de pantalla del software de configuración de VM600Mk2 (PROTECCIÓN VibroSight) que representa una medida DCDEC.
Expansión diferencial de doble canal (cono doble) DCDEDT
Cuando se utiliza una superficie cónica (en rampa) no vino, una sonda radial puede observar cambios en la holgura a medida que el eje crece o se encoge. A diferencia de una medición de vibración radial convencional, donde el espacio de la sonda no cambia a medida que el eje crece o se contrae axialmente, la superficie cónica cambiará la holgura de la sonda debido al movimiento axial. Dado que el cambio de espacio de la sonda está relacionado con el seno del ángulo del cono, el rango de una sonda dada puede abarcar una magnitud considerablemente mayor de expansión diferencial.
Por ejemplo, si el angulo del cono es de 12°, el alcance de la sonda puede abarcar aproximadamente cinco veces más expansión diferencial que si solo estuviera mirando un collar DE perpendicular.
Sin embargo, ya que la holgura de la sonda es una combinación de la posición radial del eje en la holgura del cojinete y la posición axial del cono, la señal de una sola sonda refleja ambas contribuciones. Para aislar sólo los efectos de la posición axial del cono, y no la posición radial del eje, se utiliza una segunda sonda, permitiendo restar los efectos de la posición radial del eje de las contribuciones compuestas de los cambios axiales y radiales. La segunda sonda se puede utilizar para observar un segundo cono o una parte no cónica convencional del eje..
La medida DCDEDT se representa en la Figura 5. Las superficies cónicas pueden tener un diseño convexo., como resulta, o diseño cóncavo (La llamada “mariposa”), como se muestra en el inserto.
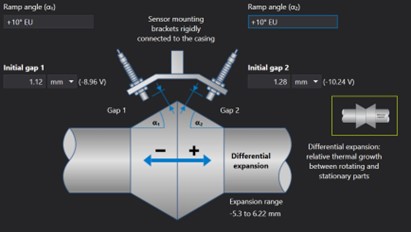
Instrumentación de supervisión de turbinas – Figura 5 Captura de pantalla del software de configuración VM600Mk2 (PROTECCIÓN VibroSight) representando una medida DCDEDT. En este caso, los conos están espalda con espalda, formando una forma convexa. La disposición de los conos se llama “mariposa” se muestra en el recuadro verde y es utilizado por algunos fabricantes de turbinas en lugar de la disposición convexa, pero las consideraciones de configuración de la sonda son esencialmente las mismas.
Expansión diferencial de doble canal (cone único) DCDEST
Esta medida es similar a la medida DCDEDT, pero utiliza una superficie radial convencional para una sonda y una superficie cónica para la otra.
Las dos sondas tienen la misma finalidad que en el caso de un doble cono, pero la sonda que mira la superficie no cónica solo contiene información sobre la posición radial, mientras que la sonda que mira al cono contiene información sobre la expansión diferencial y la posición radial. Con respecto a la figura 6, restando la señal de la sonda 2 a la señal de la sonda 1, y por trigonometría para la superficie cónica, Es posible determinar la dilatación diferencial.
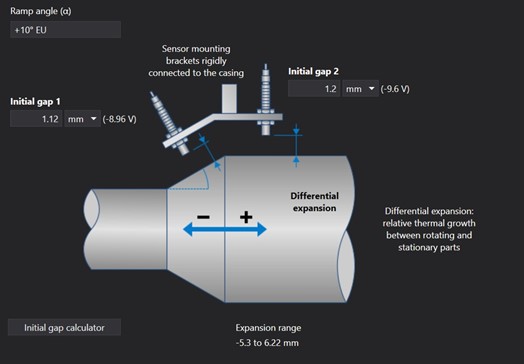
Instrumentación de supervisión de turbinas – Figura 6 Captura de pantalla del software de configuración de VM600Mk2 (PROTECCIÓN VibroSight) que representa una medida DCDEST. En este caso, la rampa esta a la izquierda.
Una nota sobre las sondas de rango extendido
Una de las razones por las que se utilizan disposiciones de DE de doble canal es que se pueden utilizar diámetros de sonda más pequeños. (con intervalos lineales correspondientemente más pequeños). en algunos casos, sin embargo, Se encuentran o se necesitan sondas DE con rangos lineales mayores que las sondas DE convencionales. 2 milímetro o 4 mm. Este suele ser el caso de las turbinas en las que se utiliza un collarín perpendicular simple en lugar de una superficie cónica.. para estas aplicaciones, a menudo se utilizan las llamadas sondas. “gama alargada” con diámetros hasta 50 mm y rangos lineales correspondientes hasta 28 milímetro Estas sondas pueden ser manejadas por el software de configuración VM600Mk2 (PROTECCIÓN VibroSight) como tipos de transductores “personalizado” Cuando se produce el contacto entre el rotor y el cojinete, por lo tanto, totalmente compatible con la plataforma VM600Mk2.
expansión del cuerpo (ÉL)
Los rotores de turbinas de vapor generalmente están unidos a un cojinete de empuje en el lado interior de la turbina de alta presión y pueden expandirse desde allí a lo largo del grupo generador de turbina.. Dado que la turbina de alta presión tiene el vapor más caliente, es el que mayor dilatación sufre y puede diseñarse para fijarse en un extremo de la caja, permitiendo que el otro extremo se expanda en los pies deslizantes de la turbina. Si uno o más pies se atascan, pueden surgir problemas como un cadáver torcido (armada) o una carcasa atascada como resultado de la fricción entre la carcasa y el rotor y/o una carcasa permanentemente deformada.
La expansión de la carcasa en turbinas grandes puede superar los 25-50 mm y se mide con mayor frecuencia con un LVDT (Figura 7) para controlar que la carcasa de la turbina se deslice correctamente (expandirse o contraerse) en tus pies.
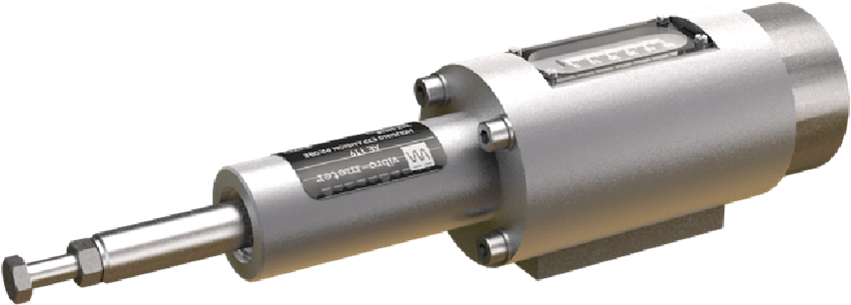
Instrumentación de supervisión de turbinas – Figura 7 El AE119 es típico de los LVDT utilizados para medidas de expansión de caja.
Las mediciones se pueden llevar al VM600Mk2 como una señal de voltaje LVDT nativa o como una señal variable de proceso casi estática de LVDT con una salida de 4-20 mA..
Si bien es posible usar un solo LVDT y tomar medidas en solo un pie de la caja, es más común equipar ambos lados con LVDT, permitiendo medir no solo los movimientos individuales, sino también la diferencia entre los dos lados. Ver a figura 8.
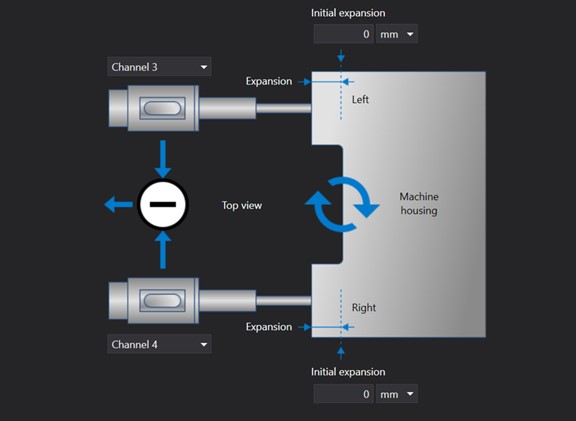
Instrumentación de supervisión de turbinas – Figura 8 Captura de pantalla del software de configuración VM600Mk2 (PROTECCIÓN VibroSight) que muestra una medida de expansión de la carcasa de dos canales (diferencial). Se mide la expansión en cada lado de la carcasa y el monitor puede mostrar estos valores absolutos., así como la diferencia entre los dos – útil para determinar cuándo un solo pie está atascado y los llamados “carcasa blindada”.
Posición de la válvula VP
Se utilizan válvulas grandes para la admisión de vapor a la turbina AP. A menudo se organizan varias válvulas en una llamada “cremallera de válvula”, donde las levas accionan disposiciones de palanca/émbolo que abren y cierran las válvulas debido a su tamaño considerable. A Figura 9 ilustra esta situación.
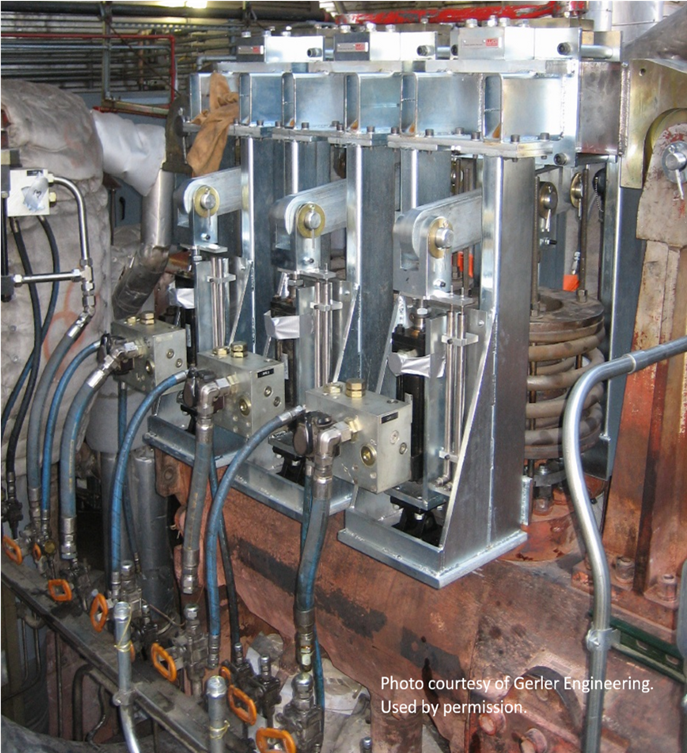
Instrumentación de supervisión de turbinas – Figura 9 Un bastidor de válvulas de turbina de vapor típico (encima).
Un método para medir la posición de la válvula es mediante el uso de un potenciómetro giratorio que detecta la posición de rotación de la leva.. Estos potenciómetros son raros y principalmente de interés histórico.. Más frecuentemente, Los LVDT se utilizan para medir la posición del carrete de la válvula (curso).
Por lo tanto, medir la posición de la válvula es similar a medir la expansión de la carcasa., en el que se utilizan LVDT para medir el movimiento lineal. Sin embargo, las condiciones ambientales en el rack de válvulas son normalmente más agresivas, tanto en términos de temperatura como de humedad, debido al vapor caliente que pasa a través de las válvulas.
Por esta razón, para mediciones de posición de válvula, Los LVDT de CA generalmente se usan en lugar de los LVDT de CC con sus clasificaciones de temperatura más bajas suficientes para las mediciones de expansión del gabinete.
En el pasado, las mediciones de posición de la válvula normalmente se incorporaron al sistema TSI. En este momento, sin embargo, esto se está volviendo menos común y las mediciones normalmente se envían directamente al sistema de control de la turbina.
La posición de la válvula en el sistema TSI es, por lo tanto, se encuentra con mayor frecuencia en situaciones de actualización donde un rack ETI más antiguo (sistema como o MMS de Vibrometer) está siendo reemplazado por un conjunto idéntico de medidas en una plataforma de hardware más nueva, como el VM600Mk2. La medida se trata como un tipo de canal cuasiestático en el módulo MPC4Mk2 y se puede realizar en cualquiera de sus 6 canales disponibles. Sin embargo, ya que la posición de la válvula no requiere procesamiento dinámico de señales, a menudo se asigna a los canales auxiliares 1 o 2.
excentricidad ECC
Dado que los rotores de las turbinas de vapor son bastante largos, si permanecen en reposo durante mucho tiempo, desviarse debido a la gravedad. En lugar de permitir que el tren de turbinas deje de girar por completo cuando la turbina de vapor no está en funcionamiento, generalmente se coloca en un engranaje giratorio (a veces llamado spinner, equipo de elevación o equipo de autobús) que gira lentamente el tren a velocidades tan bajas como 2-3 rpm, impidiendo así el desarrollo de un arco flexible.
De cualquier forma, una cierta magnitud de arco estará presente en los rotores y, durante el inicio, la longitud de este arco debe ser cuidadosamente monitoreada y controlada. Esta medida se conoce como la excentricidad del rotor. – o simplemente excentricidad – y se representa en la figura 10.
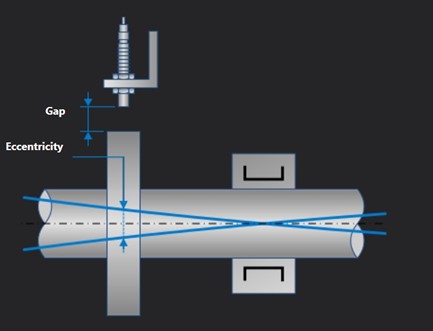
Instrumentación de supervisión de turbinas – Figura 10 Captura de pantalla del software de configuración VM600Mk2 (PROTECCIÓN VibroSight) que representa una medida de la excentricidad. A diferencia de la vibración radial, que se mide muy cerca de la ubicación de un rodamiento, la excentricidad se mide en un lugar donde cualquier curvatura residual del eje será bastante pronunciada.
Se toman medidas de excentricidad para garantizar que la cantidad de flexión no sea excesiva., permitiendo un arranque seguro dentro de los límites de vibración aceptables. En casos severos de curvatura, cuando la máquina no se detuvo por exceso de excentricidad, se sabe que los operadores doblan un rotor más allá de sus límites elásticos, resultando en un eje permanentemente doblado en lugar de una curva temporal.
La medición de la excentricidad generalmente se realiza cerca de la carcasa de la turbina de alta presión., bien alejado axialmente de un punto de apoyo o nodal y, por lo tanto, donde la excentricidad será más pronunciada y fácilmente observable (generalmente en la extensión del tubo de la turbina AP en el patrón frontal). La máquina de figuras 1.1 es, por lo tanto, típica, ya que la medida de la excentricidad se realiza en el borde exterior extremo de la caja AP, como se muestra en la Figura 1.2.
Velocidad cero ZS
Como se mencionó en la sección sobre excentricidad, la flexión del eje es una preocupación en las grandes turbinas de vapor y, por eso, se usa un engranaje giratorio en lugar de permitir que el rotor se detenga por completo cuando la turbina no está funcionando.
Los engranajes giratorios normalmente se acoplan cuando el rotor se desacelera a una velocidad aceptable. – generalmente menos de 100 rpm en unas turbinas y en otras mucho más lentas y del orden de sólo 2-3 rpm. A estas velocidades, si se utiliza una señal de referencia de fase convencional, una vez por turno, para indicar la velocidad, puede tomar hasta 30 segundos entre pulsos medidos por la sonda indicadora de velocidad.
Por esta razón, se suele utilizar una rueda dentada o un engranaje, lo que le permite actualizar la velocidad con más frecuencia y medirla con mayor precisión (no es necesario un giro completo del eje para detectar el cambio). Ver Figura 11.
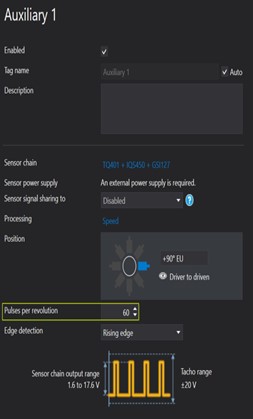
Instrumentación de supervisión de turbinas – Figura 11 Captura de pantalla del software de configuración de VM600Mk2 (PROTECCIÓN VibroSight) que representa una medida de tacómetro de un engranaje 60 dientes. Esta configuración es típica de las mediciones de velocidad cero, donde las actualizaciones rápidas apropiadas deben estar disponibles – más allá de lo que está disponible en un marcador de fase de una vez por revolución cuando una máquina está funcionando a muy bajas revoluciones.
La medición de velocidad cero es simplemente una alarma de baja velocidad que detecta cuando la velocidad de rotación ha caído por debajo de un umbral aceptable y, por lo tanto, el engranaje giratorio se puede acoplar de manera segura.. Dado que la medición es tan crítica y las implicaciones de poner en marcha un mecanismo giratorio antes de que el rotor se haya ralentizado lo suficiente son tan sustanciales, es habitual utilizar sondas redundantes y comparar las medidas de rpm de cada una para asegurarse de que coinciden dentro de un porcentaje configurable.
3 Instrumentación de supervisión de turbinas – Medidas convencionales
Todas las máquinas con cojinetes radiales y de empuje (empuje) de película fluida, se controlan mejor mediante un conjunto de mediciones que no son exclusivas de los grandes generadores de turbinas de vapor. Como tal, no se puede designar correctamente por medidas “ES”, pero son parte del conjunto total de medidas para estas máquinas. Estos se ven a continuación.
vibración relativa del eje X-Y XYSRV
Estas medidas (figura 12) se realizan con un par de sondas de proximidad rodamientos ortogonales montados cerca de cada rodamiento radial.
La disposición ortogonal de las sondas permite realizar medidas en cada plano de vibración.
Dado que las direcciones de montaje de la sonda rara vez son verdaderamente horizontales y verdaderamente verticales, generalmente se denominan X e Y en lugar de horizontal y vertical. No solo se puede medir la vibración en cada dirección, así como una medida compuesta que muestra la órbita de la vena.
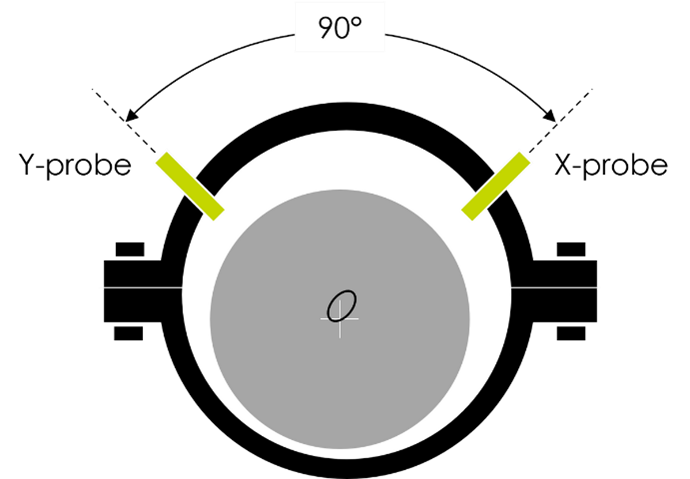
Instrumentación de supervisión de turbinas – Figura 12 – Las mediciones de vibraciones relativas al eje X-Y se llevan a cabo utilizando dos sondas de proximidad ortogonales. Éstos observan la posición instantánea del eje dentro del juego del rodamiento., en relación con la ubicación de montaje de la sonda (normalmente la caja de rodamientos).
El eje principal de la órbita se conoce como Smax y es un parámetro común calculado por el sistema de monitoreo para evaluar la severidad de la vibración. – particularmente en los países europeos. Ver también las figuras 13.1 mi 13.2.
Cuando se utiliza una sola sonda, la medición se denomina simplemente vibración relativa del eje (se omite el X-Y). Por lo general, esto no se recomienda porque solo puede observar la vibración en una dirección y es, por lo tanto, “ciego” para vibraciones en el eje ortogonal – independientemente de su gravedad.
Una sola nave espacial también limita las capacidades de diagnóstico porque ya no se puede generar una órbita junto con la información muy útil que contiene..
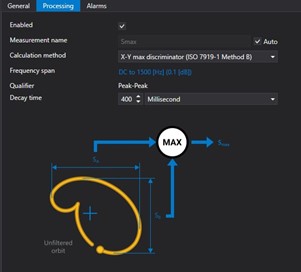
Instrumentación de supervisión de turbinas – Cifra 13.1

Instrumentación de supervisión de turbinas – Figura 13.2 Capturas de pantalla del software de configuración VM600Mk2 (PROTECCIÓN VibroSight) que representa una medición de vibración relativa al eje X-Y. Esta configuración crea un par de canales capaces de devolver no solo amplitudes individuales, pero también medidas compuestas, como smax. En este ejemplo, la sonda X está en el canal 1 e a sonda Y está no canal 2. La siguiente captura de pantalla muestra la señal compuesta de las dos sondas, resultando en una órbita del eje. El eje principal de la órbita del eje se conoce como Smax y se utiliza a menudo como parámetro de protección..
Vibración absoluta del rodamiento / Vibración absoluta del eje BAV/SAV
Las centrales térmicas normalmente emplean edificios de varios niveles con las turbinas en el último piso., permitiendo que las tuberías y la entrada de vapor asociada provengan de debajo de las turbinas. Dichos diseños a menudo dan como resultado estructuras de soporte conformes donde vibraciones sísmicas sustancial (caja de rodamientos).
Si bien esto no se limita a los grandes generadores de turbinas de vapor, es bastante tipico de ellos. para tales máquinas, es recomendable medir tanto la vibración relativa del eje X-Y, como se menciona en el punto anterior, así como la vibración de la caja de rodamientos
Aunque las mediciones de la vibración de la caja de cojinetes a menudo se realizan en el “punto muerto superior” de la tapa del cojinete y, por lo tanto, en el eje vertical puro (Figura 14), también es posible montar sensores sísmicos (esto es, velocidad o aceleración) ortogonalmente sobre el mismo eje que el(s) al final(s) de relativa proximidad al eje en el mismo rodamiento.
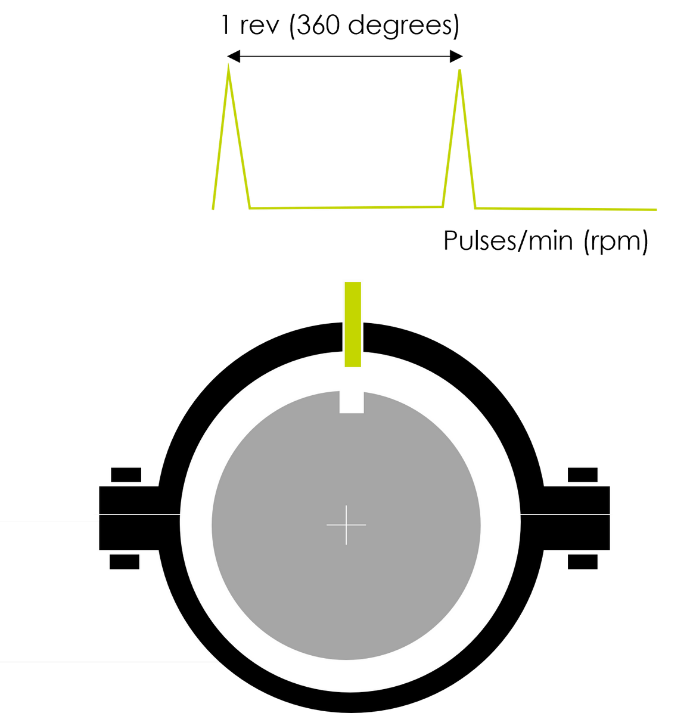
Instrumentación de supervisión de turbinas – Figura 14 – La medición de la vibración absoluta de los rodamientos implica el uso de un sensor sísmico. (velocidad o aceleración) para medir la vibración de la caja de rodamientos (o “tampa”) en relación con el espacio libre; mide solo el movimiento de la caja – no el movimiento del eje.
En esta disposición, se pueden realizar las llamadas mediciones “absolutos de la vena”, que representa la resta del movimiento sísmico de la tapa del movimiento relativo del eje.
Dado que las sondas de medición de proximidad miden el movimiento relativo combinado entre el alojamiento del cojinete y el eje, restando el movimiento de la carcasa del rodamiento, es posible aislar el movimiento del eje en relación al espacio libre y no en relación a la caja de rodamientos. Por este motivo, se describe así como una medida absoluta del eje. Ver Figura 15.
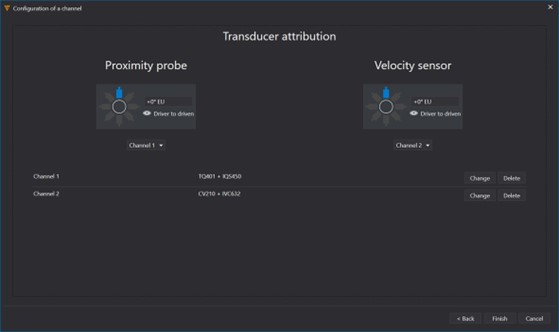
Instrumentación de supervisión de turbinas – Figura 15 – Captura de pantalla del software de configuración VM600Mk2 (PROTECCIÓN VibroSight) mostrando un par de canales usados para hacer una medición absoluta del eje. Consiste en una sonda de proximidad en el canal 1 y un sensor de velocidad en el canal 2.
posición axial (impulso) punto de acceso
Las medidas de la posición axial (ver Figura 16) se utilizan para determinar si las fuerzas de impulso están ocurriendo en la dirección esperada (o sea, normal) o en una dirección anormal (o sea, contrario) y que el rodamiento restringe adecuadamente el movimiento axial del eje.
Las fallas de los cojinetes de empuje pueden ser especialmente catastróficas porque permiten que las piezas giratorias y estacionarias entren en contacto a lo largo de toda la longitud del eje., lo que podría dañar todo el rotor y los estatores de la máquina.
Dado que esta medición es de vital importancia como parte de la estrategia de protección de la máquina, normalmente incorpora dos sondas en un arreglo de votación dual (2 en 2), donde ambas sondas deben detectar un movimiento excesivo antes de hacer sonar una alarma. Esta encuesta es requerida por el estándar API 670 para sistemas de protección de máquinas y es una buena práctica recomendada para todas las máquinas. También hay una opción de configuración para la votación 1 de 2.
USAR: Cuando las sondas axiales están unidas rígidamente a la carcasa de la máquina, en lugar de una estructura de cojinete de empuje, el efecto debido al movimiento de la estructura portante se elimina de la medición. Esto se conoce como la posición del rotor., ya que indica la cantidad de movimiento en relación con la carcasa de la máquina y no en relación con el rodamiento al que está conectado (y que también te puedes mover). Contrariamente a las mediciones del rotor en marcos que experimentan una expansión térmica significativa, se supone que la medición de la posición del rotor se realiza en marcos que exhiben una expansión térmica insignificante. Cuando la caja en sí puede experimentar expansión/contracción térmica, la sonda debe fijarse en la base de la máquina y no en su caja.
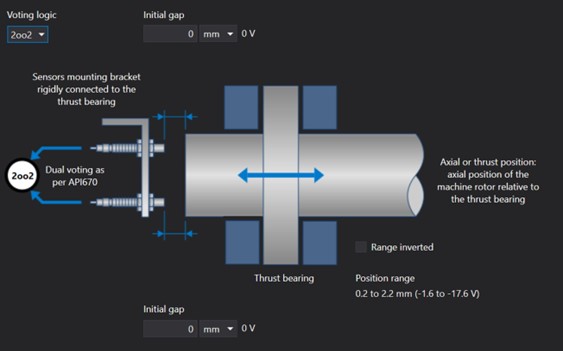
Instrumentación de supervisión de turbinas – Figura 16 Captura de pantalla del software de configuración VM600Mk2 (PROTECCIÓN VibroSight) que muestra una medición de posición axial de sondeo dual (2oo2). La votación 1oo2 también es una opción configurable, utilizando la selección de la lógica de votación adecuada en la esquina superior izquierda de la pantalla.
Disparador de fase PT
Similar a una marca de tiempo en el cigüeñal de un motor de automóvil, un sensor de disparo de fase proporciona un pulso de referencia que le permite determinar la posición de rotación (grados de rotación) de vino en un instante preciso.
Esta medición le permite calcular la fase de vibración para todas las sondas de vibración radial y sensores de cubierta de cojinete., así como medidas filtradas para múltiplos de la velocidad de funcionamiento de la máquina, como 1X, 2X, ½X, etc..
La fase es muy útil para el diagnóstico de vibraciones y es, de facto, tan útil que el diagnóstico se ve muy afectado si se pierde esta información de referencia de fase. Por esta razón, muchos usuarios prefieren instalar sondas de activación de fase redundantes para que, en caso de que la sonda primaria falle, secundaria está disponible.
A diferencia de muchas otras medidas, como un sensor de vibración radial defectuoso, un sensor de activación de fase defectuoso afecta a casi todos los demás sensores en términos de capacidades de diagnóstico de máquina disponibles. La discontinuidad de la superficie del eje para un disparador de fase es a menudo un chavetero (proyección) o un chavetero (muesca), pero a veces consiste en una ranura hecha específicamente para este propósito.
En grandes generadores de turbinas de vapor, se debe tener cuidado de colocar la marca en un lugar donde el crecimiento térmico del rotor no provoque que la discontinuidad se mueva fuera del campo observable de la sonda, como puede suceder cuando la medición se realiza en el extremo del eje, cerca del generador o conductor.
Si no hay otro lugar adecuado, la discontinuidad debe ser lo suficientemente larga para que cualquier expansión o contracción no permita que la discontinuidad abandone el campo observable de la sonda.
También se puede usar un sensor de disparo de fase para mediciones de velocidad., pero la frecuencia de actualización y la precisión no serán tan buenas como con una rueda de dientes múltiples, como se utiliza para la medición de velocidad cero. Sin embargo, esto normalmente no es una preocupación para las máquinas que funcionan a velocidades medias, como una turbina de vapor 3000 tus rpm 3600 rpm que impulsa un generador.
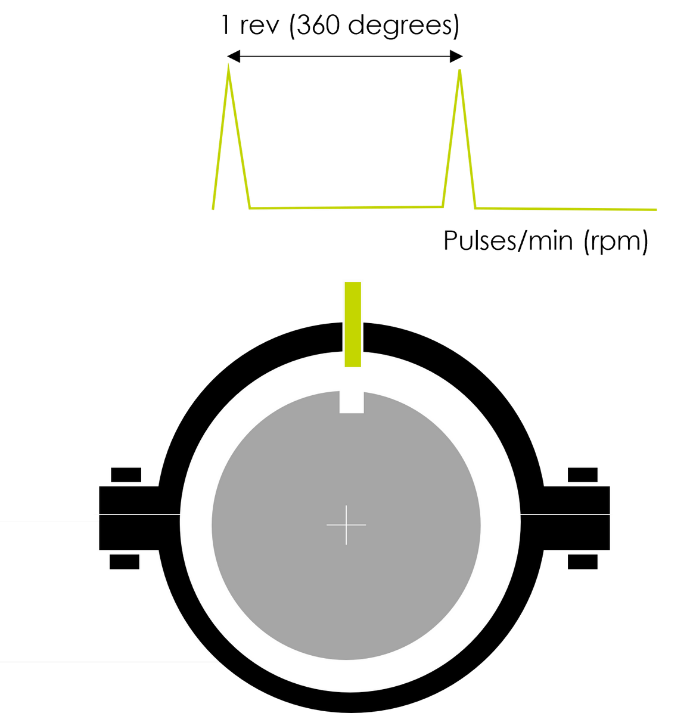
Instrumentación de supervisión de turbinas – Figura 17 Un sensor de disparo de fase (o referencia de fase) proporciona una señal de una vez por vuelta utilizada para mediciones de fase.
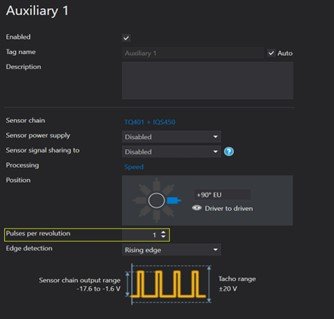
Figura 18 Captura de pantalla del software de configuración de VM600Mk2 (PROTECCIÓN VibroSight) que muestra una medida de referencia de fase. A diferencia de la configuración de la Fig. 11 (60 impulsos por rotacion), un disparador de fase real solo debe tener un solo pulso por revolución.
T temperatura del cojinete
Carga excesiva en cojinetes de película fluida – radial o axial – puede derretir el material antifricción y causar problemas importantes más allá del rodamiento, si no se detecta.
Es costumbre incorporar sensores de temperatura – RTD o termopares – en el cojinete para medir las temperaturas de las almohadillas y asegurarse de que permanezcan dentro de los límites aceptables, muy por debajo del punto de fusión de babbitt.
En este momento, las mediciones de temperatura a menudo se toman directamente en el sistema de control de la turbina, donde también pueden residir otros parámetros de protección.
Sin embargo, muchos usuarios todavía prefieren poner estas medidas en el sistema de monitoreo de vibraciones. Para éstos, el VM600Mk2 puede aceptar directamente tanto termopares como RTD a través de módulos especiales de monitoreo de temperatura. 8 canales.
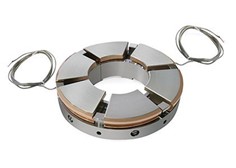
Figura 19 Un cojinete de empuje de almohada basculante típico con dos sensores de temperatura incorporados.
sobre velocidad
El exceso de velocidad de una turbina es uno de los escenarios potencialmente más catastróficos que una máquina puede soportar.. Dado que las fuerzas centrípetas que actúan sobre las piezas giratorias, como álabes de turbina y acoplamientos, están relacionados con el cuadrado de la velocidad de rotación, una turbina está diseñada para soportar solo pequeñas excursiones (20-30%) más allá de su velocidad nominal – ya sea diseñado para 50 hz (3000 rpm) o 60 hz (3600 rpm).
Cuando se producen fuerzas centrípetas excesivas, las palas pueden soltarse del rotor, convirtiéndose en proyectiles y pudiendo perforar la caja. Además, los rotores pueden doblarse, los acoplamientos pueden aflojarse y la máquina puede literalmente “explotar” (Figura 20).
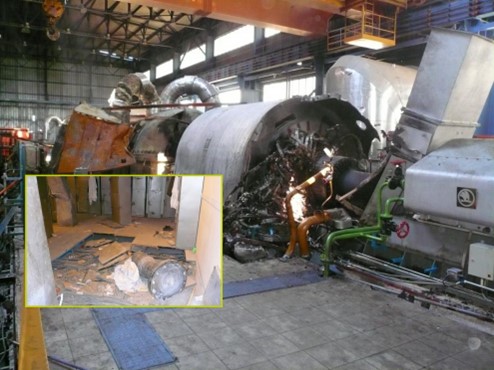
Figura 20: Consecuencias del exceso de velocidad catastrófico de un generador de turbina de vapor 64 MW. Una porción masiva de una sola pieza del carrete del eje (recuadro) atravesó una pared a muchos metros de distancia durante el evento, deteniéndose en el vestuario de hombres.
En el caso de una turbina de vapor, esto puede ser especialmente importante, porque el vapor caliente a alta presión ya no está confinado dentro del recipiente a presión (caja de la máquina) y puede infligir un daño tremendo a personas y propiedades cuando escapa.
por todas estas razones, las mediciones de sobrevelocidad son muy especializadas, involucra múltiples capas de tacómetros y sensores redundantes, a menudo en un estado de ánimo de 2 en 3 para alcanzar el nivel SIL 3.
Los canales del tacómetro de la plataforma VM600Mk2 no están destinados, por lo tanto, Mediciones de sobrevelocidad. En vez de eso, existe una plataforma SpeedSys300 (Figura 21), diseñado específicamente para aplicaciones de sobrevelocidad de turbinas.
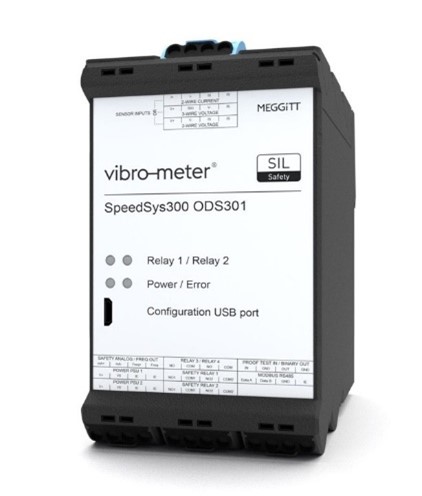
Figura 21 – O SpeedSys 300 by Vibro-meter es un sistema de detección de exceso de velocidad con clasificación SIL 3.
La mejor práctica de la industria es separar el sistema de sobrevelocidad del sistema de control de la turbina., así como el sistema de vibración de la máquina. Por lo tanto, SpeedSys300 se diseñó como una plataforma independiente para la protección contra exceso de velocidad..
3 Resumen de instrumentación de supervisión de turbinas
El VM600Mk2 está especialmente diseñado para satisfacer las necesidades de medición de la mayoría de los tipos de máquinas industriales., incluyendo turbinas de gas y vapor. Para turbinas de vapor en servicio de generación de energía, se requieren mediciones TSI especializadas y el VM600Mk2 tiene tipos de canales para cumplir con cada uno de ellos. Como la VM600Mk2 utiliza un diseño innovador de “módulo único” para proporcionar todo tipo de canales en un solo módulo (MPC4Mk2), las piezas de repuesto se reducen drásticamente.
Además de las funciones de protección de la máquina, el nuevo MPC4Mk2 incorpora capacidades de monitoreo de condición incorporadas, proporcionando toda la funcionalidad necesaria de medición en la máquina en un formato compacto 6 canales que ocupa una sola ranura en el chasis VM600.
Los usuarios pueden, así, confíe en Vibrometer para satisfacer plenamente las necesidades de estas importantes máquinas con una plataforma de segunda generación que brindará protección confiable y monitoreo de condición en las próximas décadas.
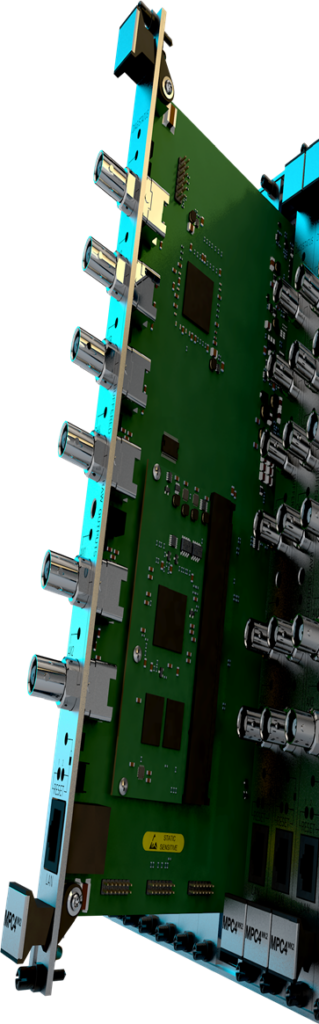