Thermography Applications
This article presents some applications of thermography and several practical cases of thermography inspection.
What is the industrial thermography?
Thermography is present in many industrial sectors, because of its potential to have a great return on investment on its implementation. industry, for example, thermography is an excellent predictive maintenance tool, enabling performing inspections securely, practical and dependable.
Through the screen, the thermal imager performs the measurement of the surface temperature of the equipment. As infrared light is invisible to the human eye, the results are displayed using colors, a temperature map.
Thermographic inspection is extremely important for the maintenance processes, it is able to identify the root of irregularities, no future, They can bring many concerns for managers, with reductions in the efficiency of the equipment, the manufacturing assembly, or even total cessation of premises.
What are the benefits of industrial thermography?
By infrared thermography, you can identify the root causes of possible failures, some of them:
- superheat;
- Overload;
- High energy consumption;
- Lack of insulation;
- loose connections and power transmission failures.
these irregularities, if not identified, controlled and corrected at an early stage, can become fault-generating, unscheduled stoppages and production losses, bringing many problems for the facilities and a lot of headaches for their managers.
As the industrial thermography can increase business productivity
With the thermographic inspections days, It is much easier to keep the focus on the three key influencers of results: risks, represented by the maintenance processes, in order to keep the equipment up and running and distant faults and stops; the time, with optimization of inspections, that can be performed without the need to disconnect the equipment; the money, cost management.
Thus, you can increase the productivity of facilities, reliability, and consequently, the useful life of equipment and achieve many positive results in the management of maintenance.
What can detect with this technique
With the condition control by thermography, can identify any problems as generating abnormal temperatures:
- wiring in poor condition
- Imbalance current / voltage between phases
- Overloaded electrical circuits
- electrical components damaged
- electric motors with low resistance
- Obstructions in heat exchangers
- Steam traps inoperative
- Leakage current in the earth cable
- Efforts in conveyor belts and transmission
- Bearing wear
- Misalignment shafts
Thermography Applications – Low voltage electrical equipment
In the following thermographic images presented, one can see thermal distributions in low voltage electrical equipment obtained with a thermography camera.


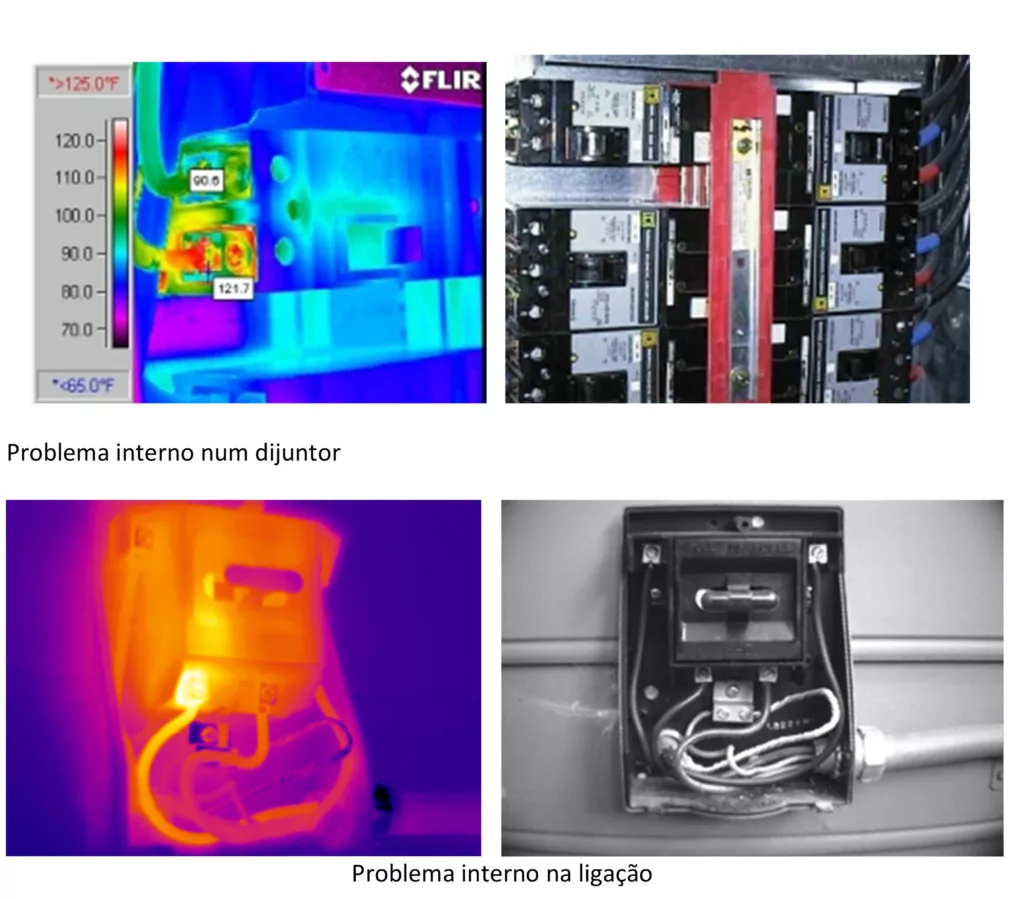
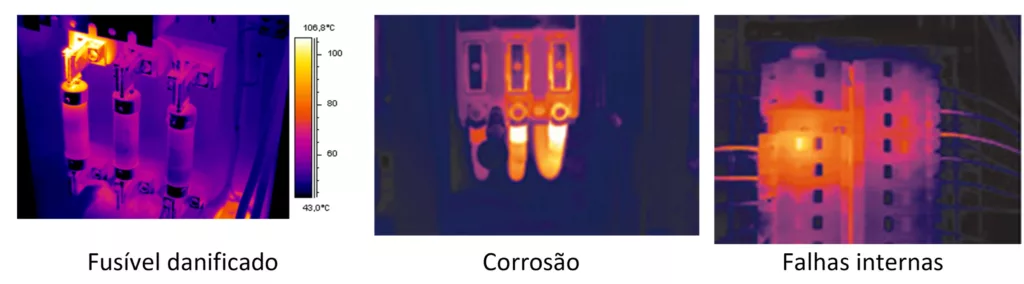



Thermography Applications – High voltage electrical equipment
In the following thermographic images presented, thermal distributions can be seen in high voltage electrical equipment.

Factors to take into account:
- Solar reflections
- Vento
- Low emissivity in metals
- Distance and size of the object to measure

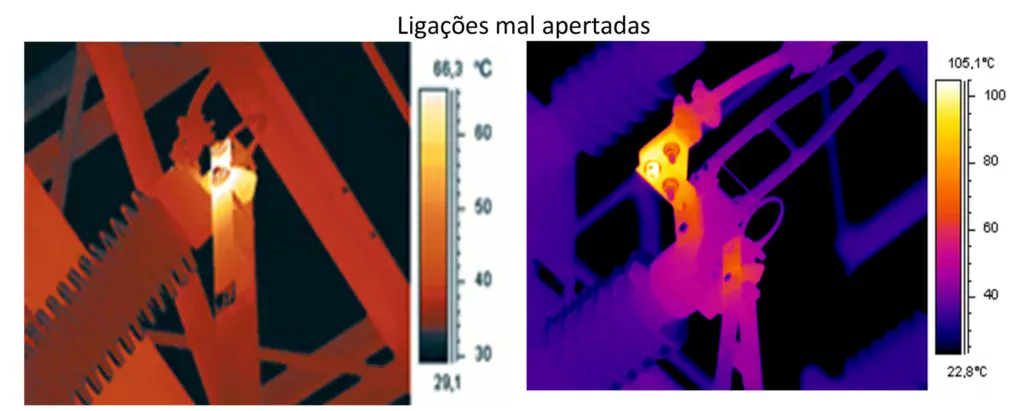


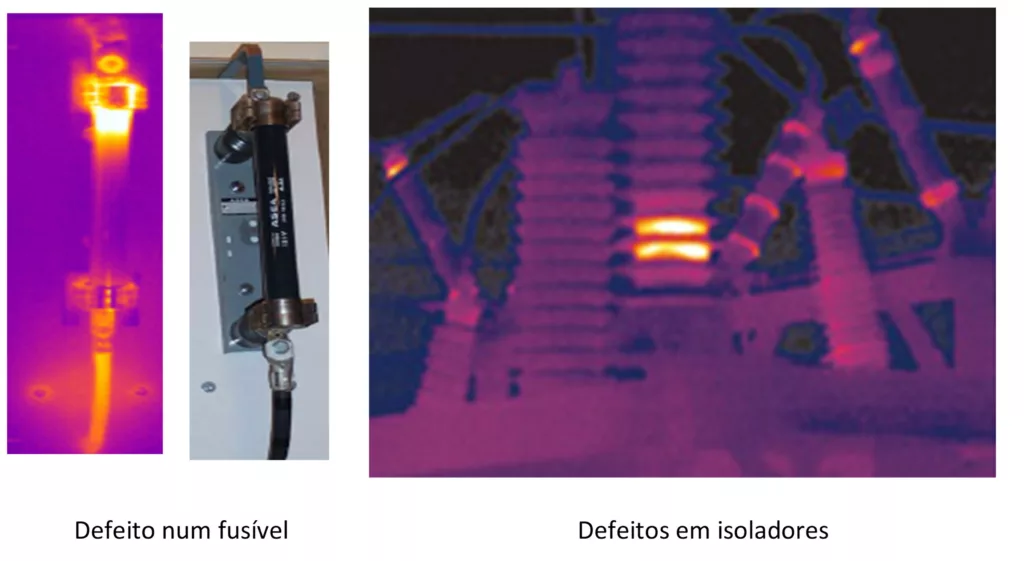
Thermography Applications – Transformers

Thermography Applications – Refractories
In the following thermographic images presented, one can see distributions in thermal equipment coated with refractory.
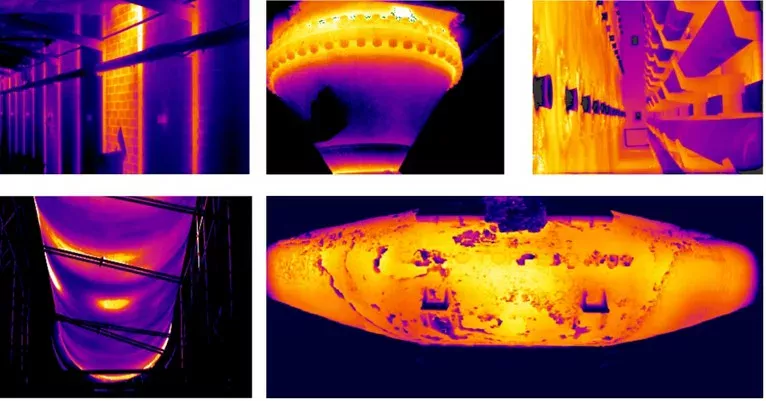
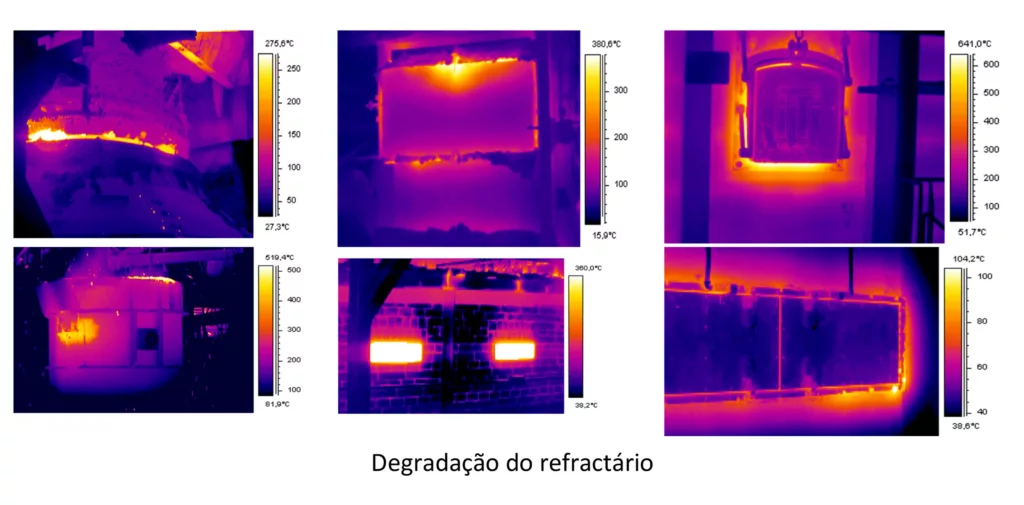
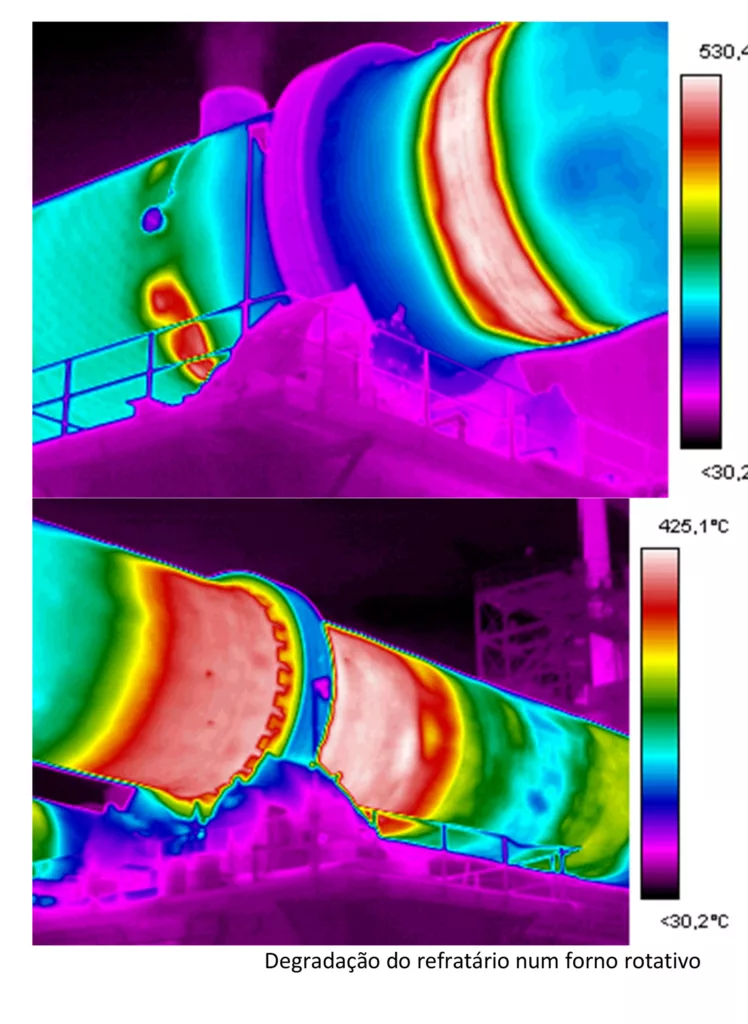
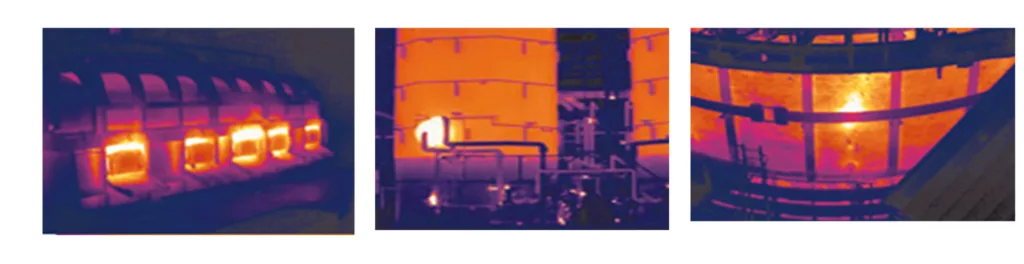
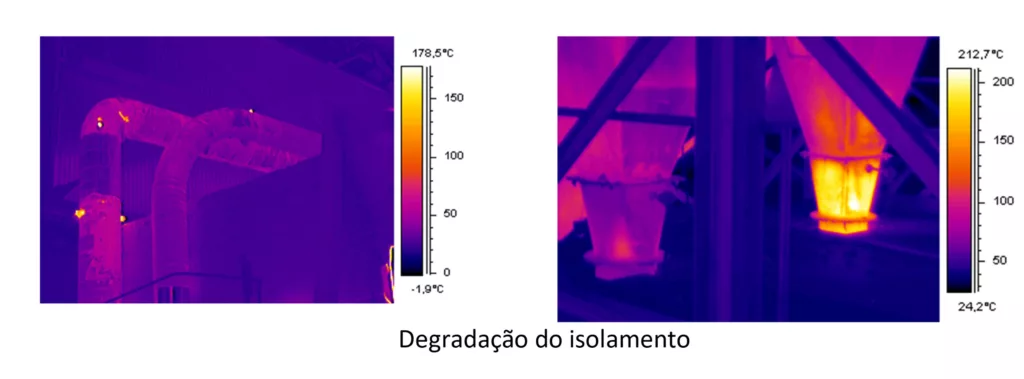
Thermography Applications – Conduits and pipes
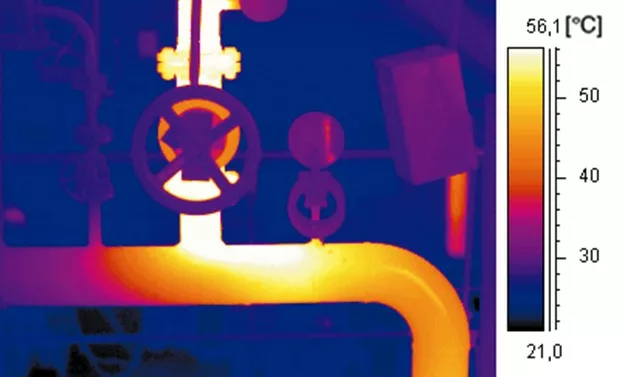
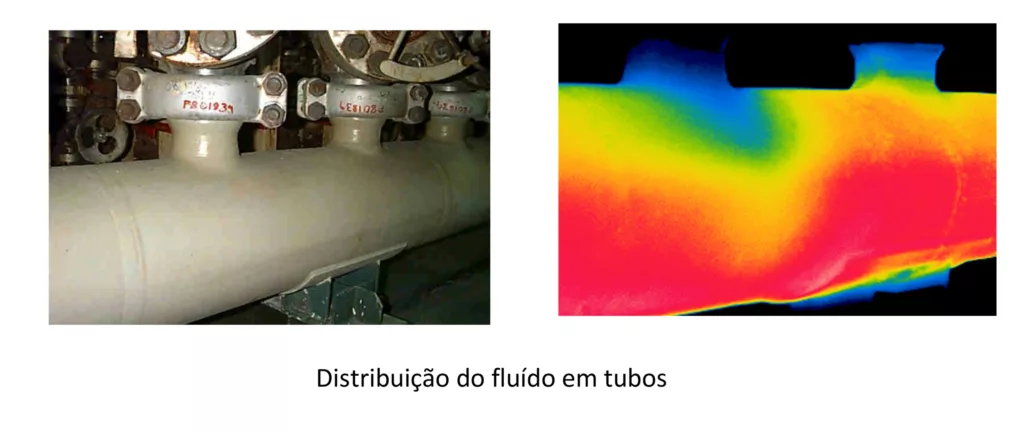
steam trap

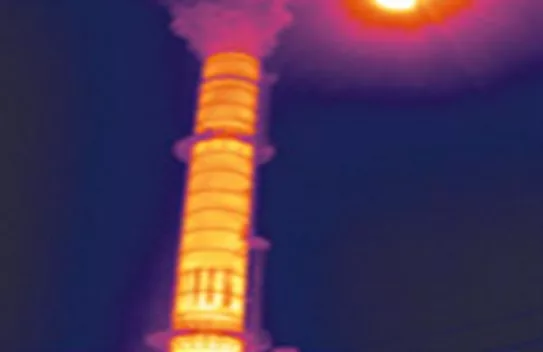
Industrial chimney inspection

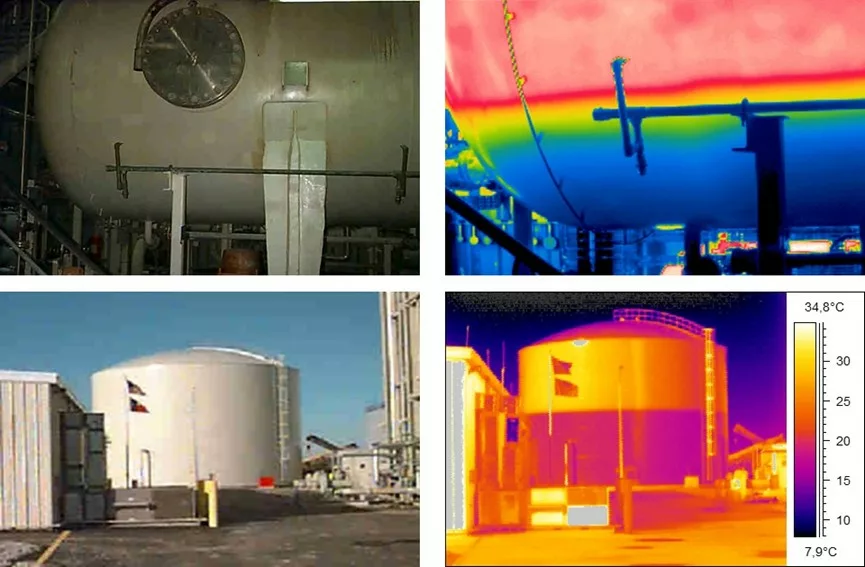
Liquid level
Thermography Applications – Asphalting


Asphalt cooling
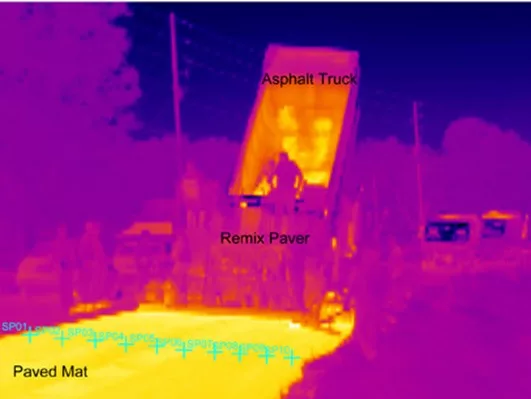
Paver
Thermography Applications – Molds
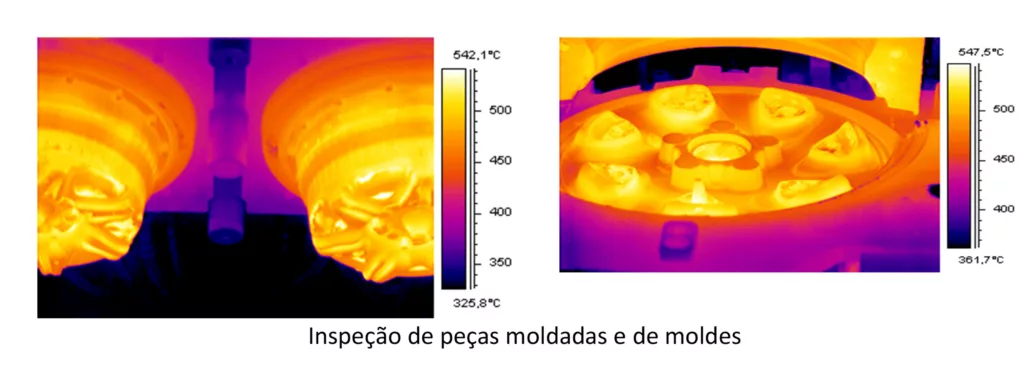
All elements can be inspected:
- Injection and expulsion
- Cooling circuits
- Molded Parts
Thermography Applications – Electric motors
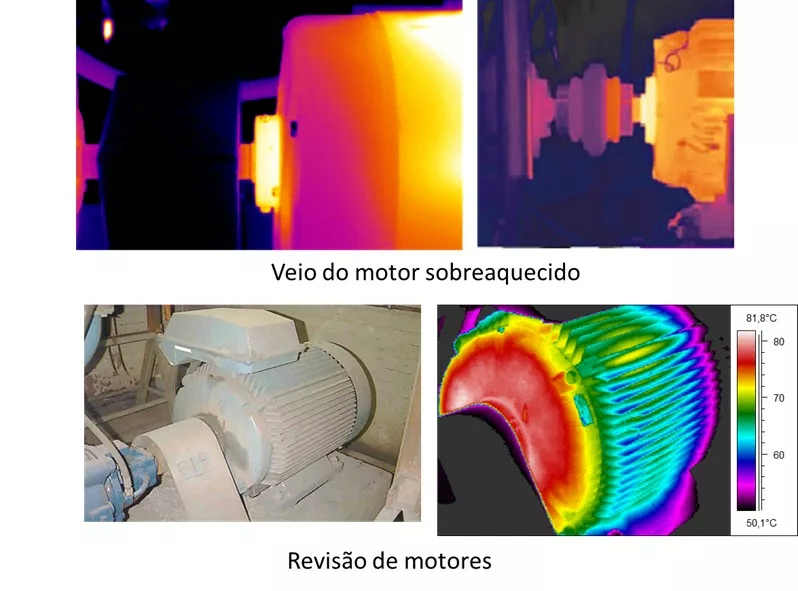
Here you can see another example.
Thermography Applications – Mechanical components
In the following thermographic images presented, one can see distributions in thermal mechanical equipment.
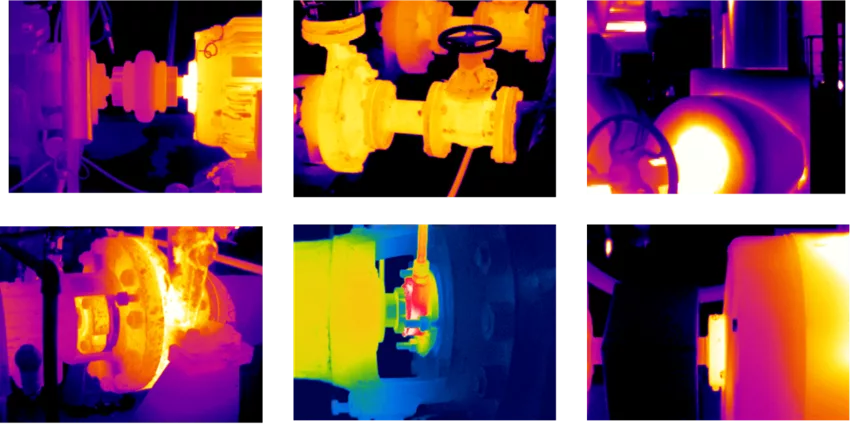
Thermography Applications- Hydraulic systems
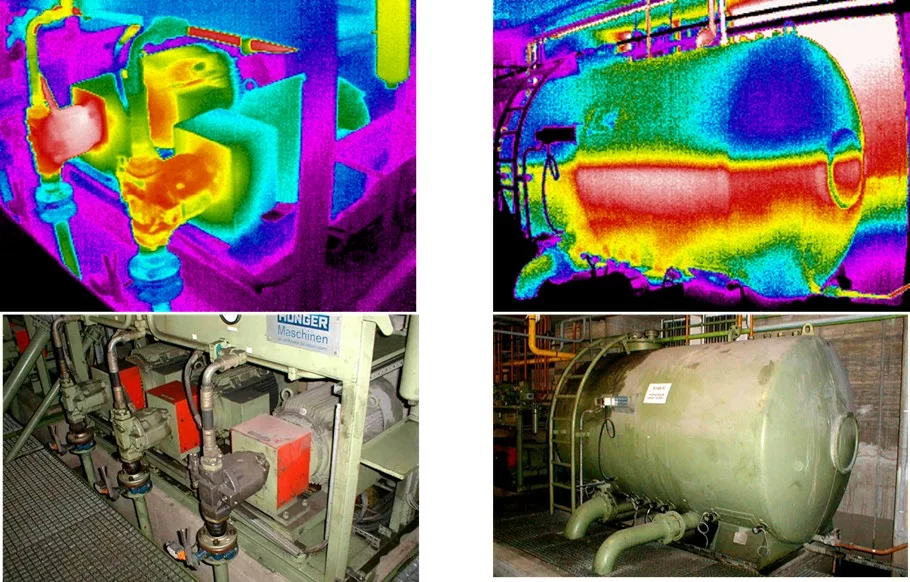
How it works
No Século XIX, It gives the discovery of the existence of infrared radiation by William Herschel .
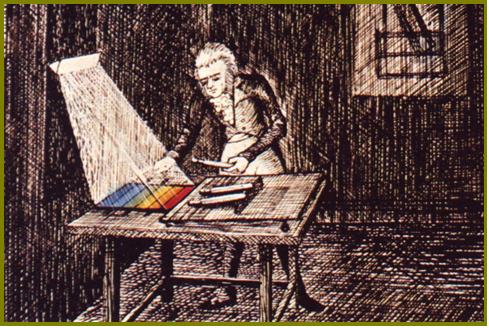
All bodies, the fact that they are at a temperature above absolute zero, emit electromagnetic radiation. Infrared thermography systems capture this radiation and convert it into an image that represents the surface temperature distribution of the observed object. The emitted radiation is given by the Stefan-Boltzmann law:
W=seT4
- W : emitted radiation
- s : Boltzmann constant (5.8 x 10-8 W m-2 K-4)
- e : emissividade
- T : temperature
The emissivity is the issue of capacity of real bodies (0 < e < 1)
Thermal imaging technique is an advanced method of non-destructive evaluation and non-intrusive. This technique involves the mapping of a body or a particular region in order to distinguish between areas at different temperatures. This technique admits, therefore, artificial viewing light in the infrared spectrum. The band of infrared is an electromagnetic frequency range, between 2μm and 13 uM wavelength, typically issued by any body, with intensity proportional to its temperature. In the following figure appears we can see the representation of the electromagnetic spectrum.
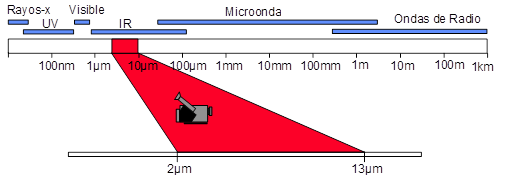
Figure 1 - wavelengths of the electromagnetic spectrum
Case 1 – Inspection of a transformer thermography
Under a maintenance contract in force, It was requested by the client inspection by thermography all transformer stations. During the inspection by thermography, found if an anomalous condition in the transformer, Having registered a temperature of 106 C. This anomaly had already caused oil spill, as can be seen in the photograph below.
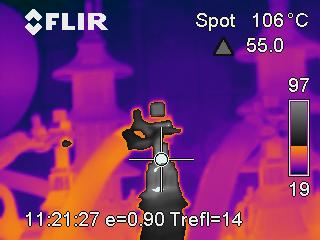
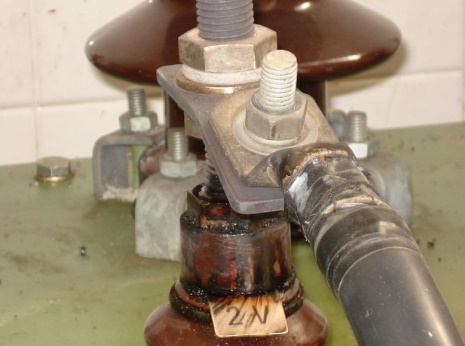
Figure 2 – Inspection by thermography – transformer
This is a critical situation that requires the immediate replacement of transformer components.
Periodic scheduling inspections by thermography is based prevent / anticipate failures or anomalies, preventing them from reaching irreversible proportions. Had it not been detected, The consequences of this anomaly could be disastrous.
Case 2 – Inspection by thermography in electrical panel
While performing the inspection by thermography to a set of electrical panels, technical DMC is faced with a situation in which the recorded absolute temperature of the components was in 163ºC. The difference in temperature relative to the ambient temperature was 136 ° C. The operating temperature had originated degradation of the cable sheath concerned.
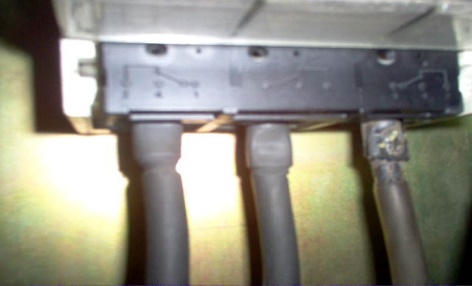
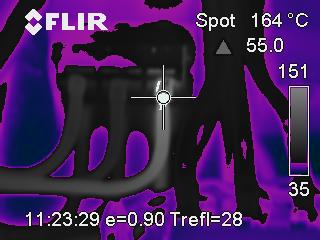
Figure 3 – Inspection by thermography in electrical panel
This is an extreme situation which led to an almost immediate maintenance intervention for cable replacement. The inspection by periodic thermal imaging would have prevented the situation had reached the proportions that have occurred, since this could have been detected in advance and, very likely, solved with a simple tightening of the cable. Its consequences, aggravated in this case because of the industry characteristic in question, could give, for example, a fire on the premises with all the consequences that this might entail.